Learn Fusion 360 in 30 Days is the most popular Fusion 360 course on the internet and was first launched in 2019. Since then, many things have changed in Fusion 360 – including a major overhaul to the user interface.
This is Day #1 of the 2023 Revised version of the course.
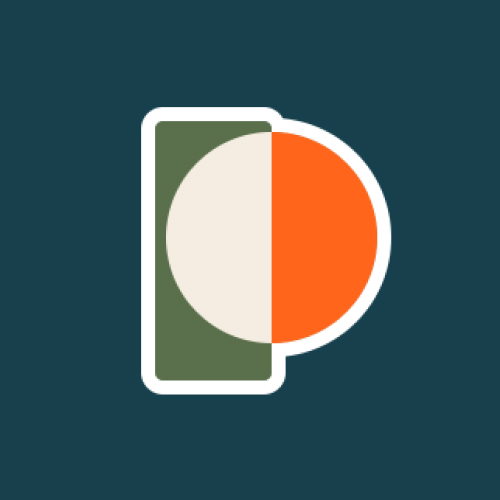
Making CAD education accessible to anyone, anywhere.
We hope you’ve been enjoying the wealth of free Fusion training provided by Product Design Online. Our commitment to empowering individuals like you with valuable skills is at the core of what we do.
If you’ve found our free content beneficial in your learning journey, we kindly ask for your support through a donation. Your contribution will not only help sustain the availability of free materials but also enable us to expand our offerings and reach even more learners globally.
Please select a donation method
Full Course on YouTube
Watch the full course in this official PDO YouTube playlist.
Transcript
Welcome to Day #1 of Learn Fusion 360 in 30 days. I’m Kevin Kennedy, and today we’ll look at how to create a 2D sketch, the Extrude feature, how to make an object hollow, and the rectangular pattern feature.
To start, select the “Show Data Panel” icon in the upper left corner. You’ll access your designs and manage projects in the Data Panel.
I encourage you to start with good habits by creating a New Project. Name this “Learn Fusion 360 in 30 Days.”
Double-click on a project to open it. Notice we can also create Folders to organize our project files. For example, I’ll make a new folder titled “Day #1 – Toy Block.”
For your convenience, I record all tutorials with Fusion 360’s default settings. You can make sure your settings are set to the defaults by selecting your profile and Preferences. Then, select the “Restore Defaults” button in the lower-left of the dialog.
If Restore Defaults is grayed out, then you’re all set!
The last thing we’ll want to do is set our default units. I’ll be using millimeters for each tutorial in this series unless stated otherwise.
On the left side, you will find Default Units for the different workspaces. We’ll select “Design” and make sure this is set to millimeters. Note that this sets the default unit for every new design file. However, you can change units of individual files at any time.
Be sure to select Apply to save the changes, before closing the dialog.
The units of an individual file are found in the Fusion 360 Browser. Toggle open the Document Settings folder and select “Change Active Units.” Select your desired units and notice you can also set the chosen units as the default. This will override the Preference that we previously looked at.
I’ll leave this set to millimeters and will close the dialog.
Let’s get started 3D modeling our toy block. You’ll want to create a new “Component” each time you start a new part. This will help keep all of our 2D sketches and 3D bodies organized. I’ll discuss more details on components throughout the course. For now, it’ll simply help keep our files organized and easier to manage.
Find the Assemble dropdown, and select “New Component”. Our type will always be a standard unless we’re working with Sheet Metal. We’ll cover sheet metal components in another lesson, as well as some of the other options.
Type out the desired part name, such as “2×8 Block.” Once complete, select OK. Notice our component is now listed in the Fusion 360 Browser.
For most Fusion 360 workflows, you’ll start by creating a 2-dimensional sketch that is turned into a 3-dimensional body.
We’ll start new 2D sketches with the “Create Sketch” feature, located in the Toolbar or the Create menu. Notice we’re then prompted to select one of the three Origin Planes. These origin planes correspond to our X, Y, and Z-axis.
I recommend selecting the plane based on how the object is sitting. We’re going to draw the length and width of the block, so we’ll select the bottom XY origin plane.
Watch closely as I select the plane.
First, you’ll see that our view is automatically reoriented to look directly at the sketch. This is because it’s generally a best practice to sketch in an orthographic or “straight on” view.
You’ll also see that we now have a Sketch tab in the toolbar. The sketch tools are contextual and will only appear while in an active sketch environment.
We can now select the 2-point rectangle tool. Once active, we’ll start by selecting the origin point. Always start at the origin as this will help us “fully define” our sketch with constraints and dimensions. We’ll be discussing this best practice in more detail throughout the course.
Notice the two-dimension inputs appear as I drag out my mouse cursor. We can select the “Tab” key on our keyboard to switch between inputs.
To simplify things, I’ll provide you with dimensions for each project. We’ll type out 15.8mm for the width of the block. Hit the Tab key, which will lock the dimension in place, and then type out 31.8mm for the length.
We can then click with the mouse to place the rectangle in the desired direction. With this particular design, the direction does not matter.
If we toggle open our Component in the Browser, you’ll find it has a “Sketches” folder. Notice this includes the sketch we just created.
We’re now ready to turn this 2D sketch into a 3D body. To make it 3-dimensional we’ll use the Extrude command, which is one of the most utilized commands in the Design workspace. You can activate Extrude from the toolbar, Create menu of the Solid tab, or by hitting the keyboard shortcut letter “E,” as in Echo.
After activating the Extrude command, you’ll be prompted to select any closed sketch profiles that you’d like to add or remove thickness.
Fusion 360 will automatically select the sketch if we only have one. We’ll define the height as 9.6mm. Notice this can be done in the Canvas or the Extrude dialog.
I’ll go ahead and hit the “Home” icon in the upper right-hand corner, located just to the left of the ViewCube. Selecting Home will give us a 3D view of our model, showing us the 9.6mm thickness.
Let’s select OK to confirm the Extrude. Notice our 3D body is now listed in our Component. Everything is nicely organized and we can toggle the visibility of any of these, at any time.
You’ll also find our actions are being recorded in the parametric timeline, at the bottom of your screen. This allows us to go back and edit, or delete features at any time.
At this point, we must save our work. Fusion 360 is cloud-based, which simply means your files are stored on Autodesk servers instead of your local computer.
We’ll still want to select the Save icon in the Applications bar. You can then define both the file name and the location of the file, or where it lives in the Data Panel. Selecting the caret icon will allow you to navigate through your projects and folders. Select “Save” and watch what happens to the design tab.
You’ll see the name of the file and the version number will appear in the design tab. We’ll talk about versioning in another lesson. Let’s go ahead and finish off the toy block with the circles on top.
We’ll start by drawing a 2D circle on the top. Once again, we’ll use “Create Sketch” to start a new 2D sketch. This time, we’ll select the top planar face of the block.
Select the Center Diameter Circle or use the keyboard shortcut letter “C,” as in Charlie.
You’ll select once to place the center of the circle, not worrying about where you select. We can then define the diameter as 5mm and select again to place the circle.
Notice each sketch command remains active until you press the Escape key.
At this point, our circle can still move freely if we select and drag it. We’ll use sketch dimensions to limit its degrees of freedom.
Select the Dimension tool in the toolbar. We’ll select the center of the circle and then the top edge of the rectangle. Notice as I drag out with my mouse we see a dimension. Select again to place the dimension and then define its value as 3.9mm.
Let’s repeat the previous steps in the other direction, also entering 3.9mm for the distance.
At this point, we could manually draw all of the other circles, but it would be much more efficient to use the Rectangular Pattern feature. It’s important to note that Fusion 360 has both a sketch Rectangular Pattern feature and solid modeling Rectangular Pattern feature. I recommend avoiding the sketch one at all costs. Keeping our sketches simple will make it much easier to have a fully parametric model.
We’ll instead activate the Extrude command with the shortcut letter “E.” I’ll select the circle and define the distance as 1.7mm. Before clicking OK, notice the Operation is set to Join. This means this new Extrude will join the existing 3D body.
We can now use the Solid modeling Rectangular Pattern feature, located in the toolbar or Create dropdown.
The pattern “Type” will determine what we can choose to pattern. It defaulted to “faces,” but we’ll want to change this to “features.” Features will allow us to select the Extrude feature in the parametric timeline. You’ll notice the cylinder turns blue when it’s selected.
Switch to the direction selector, where we’ll select two edges to define the directions for the pattern. Select both edges of the block.
Notice we have two directional arrows on the model. Drag each one to get the pattern started. Dragging them first helps ensure we’re heading in the right direction before defining the numbers in the dialog.
For the length, I’ll type 24mm for the distance, with a quantity of four. The second direction will be a quantity of two, with a distance of 8mm. Note that you may need to add or remove the minus symbol to keep the pattern in the right direction.
If the preview looks correct, then we’re all set and can click OK. If yours is off, double-check the “Distance Type” is set to “Extent.” We’ll discuss that more in additional lessons.
We’re just about done with our toy block. If you use the ViewCube to look at the bottom, you’ll see that we still have a solid block. We can use the Shell command to hollow out solid 3D bodies.
Shell lives in the Modify menu or the toolbar. We can select faces or bodies, which determine how the object is hollowed out. Because we want to leave the outer four walls, we’ll select only the bottom face of the 3D body.
We then define the “Inside Thickness” which is 1.49mm. Shell traces the outside walls of the design and applies our defined thickness. That is why you’ll see the inside of our cylinders were included.
Click OK to confirm the Shell.
Lastly, we’ll draw the three center columns at the bottom of the block.
You can also create new sketches by right-clicking on a planar face, followed by “Create Sketch.”
Let’s activate the Line command from the toolbar.
We’ll start by selecting the “Construction” option in the Sketch Palette, as this line is for reference purposes only.
Then, because we’re looking at an orthographic straight-on view, you’ll find we can reference some of the existing geometry. Referencing our model’s geometry will not work if you look at the model from an angle.
To create this line I will move my mouse cursor over these recessed circles. You’ll see that it lets us snap into their center point. Then, I’ll draw the line across to the other side, snapping it into the other center point. Press Escape to clear the line command.
With the Center Diameter Circle, we now have a reference line to find the midpoint. Be sure to turn off the construction option in the dialog box, or by pressing the keyboard shortcut letter “X.”
Find the midpoint where the triangle glyph appears. After we place the circle, we can define the diameter as 6.3mm.
As an alternative to the Shell command, sometimes we may want to Extrude an object with two defined walls.
We can use the Offset sketch tool from the Toolbar. Select the circle and type out 1mm for the offset distance. Flip the circle to make sure it’s on the inside.
We can now use Extrude to turn this cylinder into a 3D body. Let’s define the distance as 8.1mm.
Once again, let’s use the Rectangular Pattern feature. The pattern type should be set to “Features,” as we used that last. Select the latest Extrude in the timeline below.
Select the edge for the direction.
I’ll type 3 for the quantity and 16mm for the distance and click OK.
If you now revolve the toy block around, you’ll see that we have completed the overall shape.
The last thing we’ll want to do is add a Fillet, or rounded edges, to some of the sharp edges.
Activate the Fillet command from the Modify dropdown list or by selecting the keyboard shortcut letter “F,” as in Foxtrot. Select the edges or faces to Fillet and add a Fillet of 0.2mm by typing that out in the dialog box.
Be sure to save your design once you’re finished. Notice it will prompt you to add a “Version Description” with the version number. Something like “Finished the toy block” will be helpful.
You’ll see the version number updates in your design tab.
[Upbeat Music]
I’ll see you in the next lesson where we’ll look at 3D modeling a glass soda bottle.
[End Upbeat Music]