When determining the software you want to use, it’s important to know what you will be designing. Are you designing manufacturable parts or organic objects, such as mini-figures?
Most CAD software leans one way or the other. Providing you with the accuracy and precision to design parts or the creative freedom to sculpt from your imagination.
CAD programs are often grouped, but there are many different types of 3D modeling software.
Autodesk Fusion (formerly ‘Fusion 360’) is unique in that it offers two different types of modeling – Parametric and Direct Editing.
Parametric Modeling
First and foremost, Fusion is a parametric modeling software. Parametric modeling is a CAD approach in which the user defines features and constraints with design intent in mind. Every part of a model is created to exact dimensions when using parametric modeling. Dimensions can be updated or altered at any time because they’re recorded in the parametric timelineThe timeline lists operations performed on your design. Right-click operations in the timeline to make changes. Drag operations to change the order they are calculated. More.
In Autodesk Fusion, parametric designs most often start with a 2D sketch that is anchored (or “constrained”) to the origin pointCreates a sketch point. More. Once a sketch is fully defined, the Create tools (ExtrudeAdds depth to a closed sketch profile or planar face. Select the profile or planar face then specify the distance to extrude. More, RevolveRevolves a sketch profile or planar face around a selected axis. Select a profile or planar face then select the axis to revolve around. More, SweepSweeps a sketch profile or planar face along a selected path. Select a series of profiles or planar faces to define a shape. Optionally select rails or a centerline guide the shape. More, etc.) turn the sketch into a 3D body. Users can then modify the 3D body with additional features or create another 2D sketch before creating additional 3D bodies.
The process of fully defining the sketches and features will help the model remain predictable per the creators’ design intent – or a plan so that a change to one propagates automatically to others.
Pros of parametric Modeling
Every parameter (dimension or constraint) of the model is defined, which makes it easy to go back and alter or update the model based on new requirements. It is also possible to set variables so that by updating one value the rest of the dimensions using that variable are automatically updated.
The parametric timeline is seen at the bottom of Autodesk Fusion and shows the user the linear series of steps that they made. This makes it easy to go back to an earlier point in the model. Change or remove features while maintaining the design intent of the 3D model.
Parametric models include a high degree of accuracy since each dimension is set by the user. This makes parametric modeling ideal for Product Design, Industrial Design, or Mechanical Engineering.
Cons of Parametric Modeling
The parametric modeling process requires inputs, constraints, and dimensions for every piece of sketch geometry, as well as each 3D feature. Depending on the project’s needs, it can be time-consuming and repetitive to make the model fully parametric.
Parametric models are dependent on the order of operations in which features are applied. This can sometimes cause errors or issues if one makes changes to earlier parts of the model. Downstream parts of geometry can become broken or altered.
Errors and timeline warnings frequently happen when trying to remove parts of the model that were used with constraints, or when a sketch plane no longer has a planar surface or 3D body to reference.
Projects to Try
Parametric modeling is perfect for any mechanical or product design projectProjects the body silhouette, edges, work geometries and sketch curves into the active sketch plane. Use the selection filter to project a specific type of geometry or the body silhouette. More, where dimensions and scaleScales sketch objects, bodies, or components. Select the objects to scale then specify the scale factor. More are of utmost importance. When tolerances are too loose or too tight the model can be quickly tweaked. The precise geometry ensures you have complete control over the size, shape, and tolerances of the part.
A simple project I would recommend is our parametric dovetail box with a sliding lid. This would allow you to design a functional 3D printConverts the selected body to a mesh body and outputs to STL or a 3D print utility (software). Select the body to output. Set the mesh controls and specify the print utility to output to. More that can adapt to the size of your project needs.
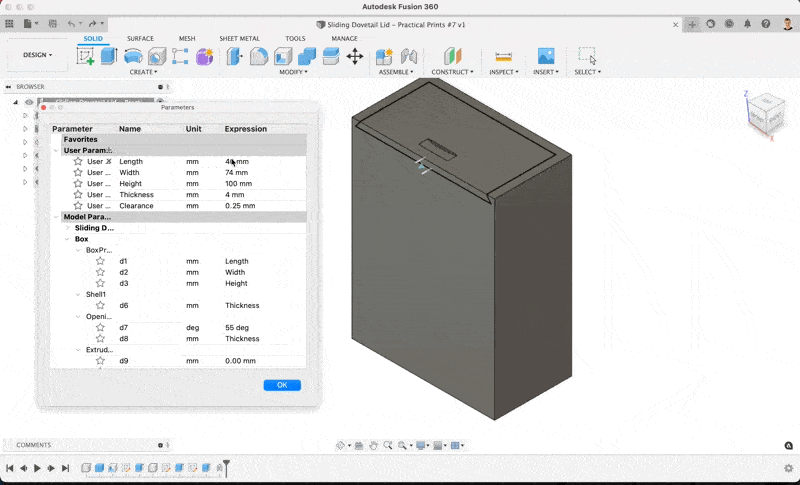
Direct Modeling
Autodesk Fusion also offers Direct Modeling. Direct modeling is non-parametric, which means users can manipulate 3D bodies by pushing, pulling, or twisting – without ever recording features in the parametric timeline.
To enter Fusion’s direct modeling mode the user must first disable the timeline by right-clicking on the root (top-level) component, followed by “Do Not Capture Design History.”
Turning off design history will allow the user to work with models in a direct editing mode, including the ability to push and pull on faces, edges, and vertices.
Most importantly, any changes made in direct edit mode are not recorded in the parametric timeline. This can prove to be challenging if one needs to update dimensions later on.
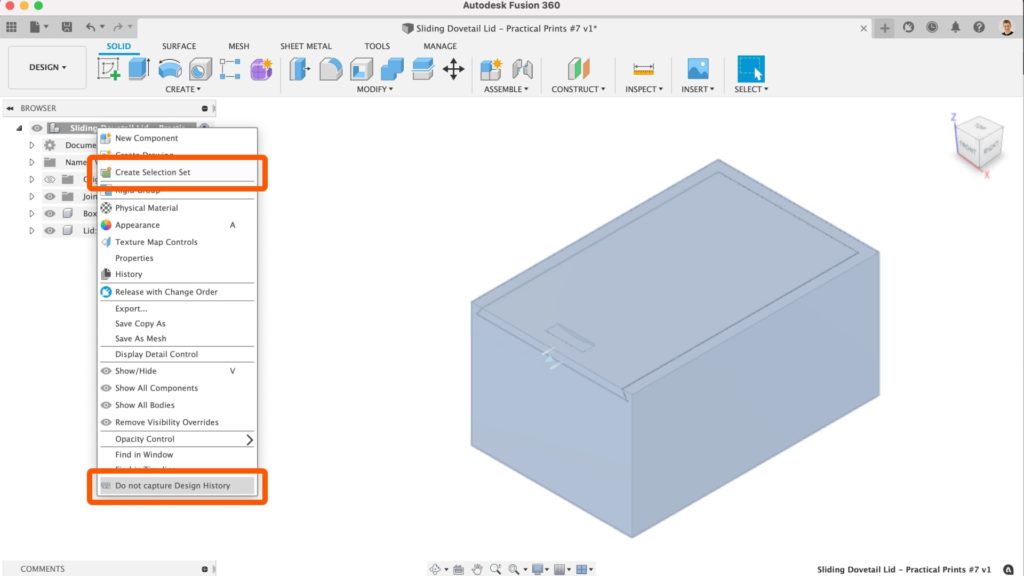
Pros of Direct Modeling
Some projects may be significantly faster to 3D model in direct modeling mode versus parametric mode. Ultimately, each project should have consideration for future needs. Spending extra time at the beginning of the project may help reduce wasted time later on.
The decision between parametric and direct editing modes is not always easy. Fortunately, parametric designs can always be converted to a direct editing mode. However, direct edit design files cannot be converted to a parametric design (without having an empty timeline).
Direct modeling is often compared to working with modeling clay. But don’t be fooled, the feature sets in Autodesk Fusion still function the same – it will simply save(keyboard shortcut CMD/CTRL+S) Saves the file that is currently open. More you time worrying about features, constraints, and original design intent. Simply push and pull the model’s geometry until you arrive at the desired shape.
Cons of Direct Modeling
The biggest downside to direct modeling is that features cannot be quickly modified or updated in a parametric manner. To be clear, you can still edit or modify previously made 3D bodies, faces, etc. You will not be able to have sequential features automatically updated from a single change.
Projects to Try
Try modeling the same dovetail boxCreates a solid box. Select a plane, draw a rectangle then specify the height of the box. More with a sliding lid that we shared above. Compare the time it takes via direct modeling versus parametric modeling. You may find it to take far less time on the first pass; however, updating the size and geometry may prove to make parametric modeling the superior method.
[…] 360 is a parametric CAD/CAM/CAE software package, most known for its modern user interface and versatile feature set. You may be […]