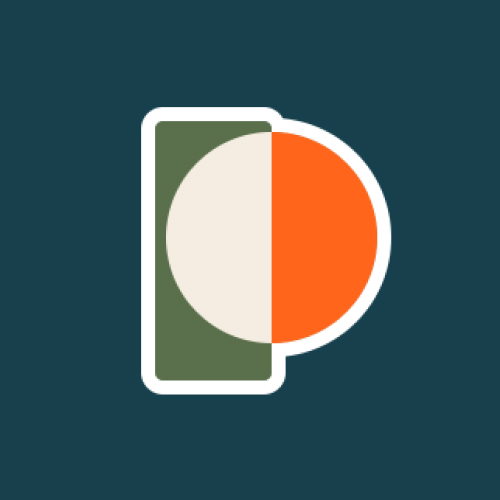
Making CAD education accessible to anyone, anywhere.
We hope you’ve been enjoying the wealth of free Fusion training provided by Product Design Online. Our commitment to empowering individuals like you with valuable skills is at the core of what we do.
If you’ve found our free content beneficial in your learning journey, we kindly ask for your support through a donation. Your contribution will not only help sustain the availability of free materials but also enable us to expand our offerings and reach even more learners globally.
Please select a donation method
Full Course on YouTube
Watch the full course in this official PDO YouTube playlist.
Soda Bottle Reference Image
To follow along with Day #2 – select ‘Download Image’ below to save the Glass Soda Bottle reference image. Alternatively, right-click on the image below > Save As > save to your Desktop or Downloads folder.

Transcript
Welcome to Day #2 of Learn Fusion 360 in 30 days. I’m Kevin Kennedy,
and today we’ll create a glass soda bottle as you learn to insert a reference image, create a fit-point-spline, use the revolve feature, and add the appearance of glass.
Let’s start by saving our design. Fusion 360 files are saved “in the cloud,” but we must select save and name the file at the start of each new design file.
Type out the desired name, such as “Glass Soda Bottle.”
Notice we can also toggle the location dropdown, which allows us to see the same projects and folders we set up on Day 1.
Select the correct project on the left if yours is not already selected. I’ll create a “New Folder” for Day 2 – Soda Bottle. Double-click to select the folder, and notice this will update the location the file is saved.
After we select Save, we’ll want to start with a “New Component.” A component will group all of the images, 3D bodies, and other information into a “folder” in the Fusion 360 browser. This is something we’ll discuss in greater detail when we get to multi-part assemblies. For now, let’s get into the habit of creating a new component for each unique part.
Name this “Bottle” and click OK.
Starting your file with a reference image can be a great way to reverse-engineer designs.
You will find the Canvas feature in Fusion 360’s toolbar. It’s also located in the “Insert” menu. Once active, we can choose an existing reference image from our Projects and Folders, or we can select “Insert From My Computer” to choose one from our local machine.
Select the reference image which you can download below this video.
We then need to select the origin plane or an existing planar face to place the reference image on.
This reference image is the “Front” view of the bottle, so I’ll select the corresponding “Front” origin plane.
Notice we now have a number of options to alter the reference image, including changing opacity, scale, flipping, and more. You may also use the manipulators on the image to scale or stretch the image.
We’re going to click OK, without worrying about the correct size.
We’ll instead use the ‘Calibrate’ tool to precisely scale the image.
Toggle open the “Bottle” component, followed by the “Canvases” folder. It’s here you’ll see the image that we just placed.
Right-clicking on the image will allow us to select the “Calibrate” tool.
Select the approximate bottom of the bottle, followed by the top. Notice we can then define the dimension between the two.
I’ll type out 240mm, and watch what happens as I press the “Return” key. You’ll notice the image automatically scales to the exact size. We’ll now be able to trace the image, creating our model at a 1-to-1 scale. Designing to scale is important if planning to 3D print or manufacture the design.
We can use the Home Icon next to the ViewCube, or simply Zoom out to see the whole image.
Fusion 360 automatically hid the Origin planes, so let’s turn them back on by selecting the eyeball icon in the Browser. You’ll see that the origin is currently in the middle of the image. Generally, I like to move the image so the bottom aligns with the origin point, making it an easier starting point.
At any point in the design process, right-click on the Canvas in the Browser and select “Edit Canvas”. We can then use the center square to freely move the image around.
Align the bottom center of the bottle to Fusion 360’s origin point, then click OK.
Our reference image is all set and we can now start sketching the 2D outline, which we’ll soon turn into a 3D body using the Revolve tool.
Right-click on the Front Origin plane and select “Create Sketch.” Once in the Sketch environment, activate the Line tool from the toolbar.
Start the line by selecting the origin point. We’re going to make this line run straight up the bottle at the same distance of 240mm.
Before selecting to place the line, make sure you see the Vertical Sketch Constraint icon. This icon lets us know the line will snap in the vertical direction. Sketch Constraints are a critical part of parametric design and something we’ll discuss a lot throughout this course.
Press the Escape key to clear out the Line command so we can start a line in a new location.
Activate Line again, and let’s draw a second line starting at the origin point. This time, we’ll head to the right 30mm, making sure it snaps in horizontally.
Keep in mind the bottle in our reference image is at a slight angle. We want our bottle to have a flat bottom. We’ll also add the rounded edges in just a minute.
Notice the Line command remains active. We can continue by sketching a vertical line with a distance of 130mm. Be sure to type out each dimension, followed by the Return key. Simply selecting to place the line will not save a dimension.
We’ll now use the “Fit Point Spline” tool to sketch the curvature of the stem of the bottle.
Activate it from the Toolbar.
Start by selecting the end point of our vertical line. When sketching splines, you’ll want to select to place each point where the curvature changes in direction. It’s considered a best practice to use the least amount of “Fit Points” as possible. This will help you maintain smooth and realistic geometry.
Take your time to select each point where the curvature changes, keeping the points to a minimum. Keep in mind this does not have to be perfect, as we can adjust the points after.
Once you’re done placing the points, you’ll want to hit the Return key or you can select the green checkmark icon.
It’s important to note that you cannot hit the Escape key after creating your last spline point. Although the Escape key exits most sketch commands, it will delete spline geometry that is not confirmed.
After completing a Fit Point Spline, take time to adjust the points and their handles so they match the reference image.
You can also click and drag spline points to move them around.
To get the spline handles of one point to appear you can select the line or an individual point. You can then click and drag on the handle to adjust the curvature.
This does take some trial and error, so don’t be afraid to practice, and hit “undo” if you need to revert any mistakes.
One critical thing we’ll want to do is make sure the starting point of our spline has a smooth transition to the straight line. We can do this by selecting the bottom fit point, and then select the handle of the point. Once selected, we’ll choose the vertical constraint, which forces this to remain vertical, lying in the same direction as our vertical line. This will ensure we have a smooth transition.
We can now create a line segment that connects the top two endpoints. Zoom in on this section, which will make it easier to work with.
After drawing your line, make sure you have either a perpendicular constraint or a horizontal constraint that was automatically applied. If not, go ahead and add one. This will ensure the top of our bottle remains level.
After fully connecting our shape, you may have noticed that our shape now has a blue background highlight. Blue signifies that we can use the profile shape with the Solid modeling commands. Many commands, such as the Revolve command, require at least one closed sketch profile.
As you go to activate the Revolve command, it’s important to make sure you activate it from the “SOLID” tab in the toolbar, which has blue icons. Do not select Revolve from the “SURFACE” tab, or the orange icons. We’ll discuss surface modeling later in this course.
With many of Fusion 360’s features, the software will take an educated guess as to what you’re trying to achieve. In this case, you’ll find it automatically selected the profile for us, since we only have one profile. If not, you can go ahead and select it.
Following the items in the dialog, you’ll see we need to select the center Axis. This axis will tell Fusion 360 how to revolve the profile shape, so we’ll select the center line of the bottle.
Notice we now have a 3-dimensional shape. Revolves are generally done at 360 degrees to complete the object. However, in some scenarios, you may find it necessary to alter the degrees.
We can now click OK to save the Revolve.
At this point, we can turn off the Canvas or Reference image in the Browser.
You may be wondering why there are lines down the side of the model. This is simply the default visual style setting, which shows visual edge lines. It does not affect the 3D model itself.
You can change this Visual Style option to “Shaded” to see what the bottle would look like. This can be helpful to inspect the curvature of your designs.
I’ll change this back to the default, which is also my personal preference.
Let’s activate the Fillet command to add a 5mm rounded edge to the lower edge of the bottle. This will round over the sharp edge.
It’s important to note that we’re adding the Fillet before we make the bottle hollow, as the “Shell” command will trace the inside of the object.
I also want to make sure the opening of the bottle is the correct size. I’m going to double-click on the sketch in the timeline. Parametric modeling allows us to go back and edit previous actions at any time throughout the design process.
Activate the Sketch Dimension tool and apply a dimension to the top, making this 11mm. Notice the sketch will adapt to the newly defined dimension. It will also remain horizontal thanks to the horizontal sketch constraint.
Activate the Shell command from the toolbar. If you recall on Day 1 we used Shell to hollow out the Toy Brick. We’ll do the same thing to the bottle by selecting the top of the bottle. Define the Shell thickness as 2.5mm.
Shell will trace the contour of the body and apply our defined thickness. If you do happen to get an error message, it’s likely due to the thickness not being appropriate for the geometry of your bottle. Edit your sketch and adjust the stem of the bottle until the Shell command works. Alternatively, you can adjust the desired thickness in the Shell command.
I’m also going to add a 1mm fillet to the top two edges of the bottle, to ensure they’re not sharp.
Once complete, we can activate the “Appearance” command from the Modify dropdown menu.
Appearances are visual representations of materials that will help you better visualize your designs. Appearance can also be activated with the shortcut letter “A,” as in Alpha.
Once active, search through the available materials. Find the Glass folder and drag and drop the material over to your design. Note that you will need to download each material the first time you go to use it.
The appearance of glass helps us better see the thickness created by the Shell command.
Experiment with some different Shell thicknesses to see how it changes.
[Start Upbeat Music]
You’ve successfully completed the soda bottle design! Don’t forget to save your design and I’ll see you on Day 3, where you’ll learn how to sweep a paperclip!
[End Upbeat Music]