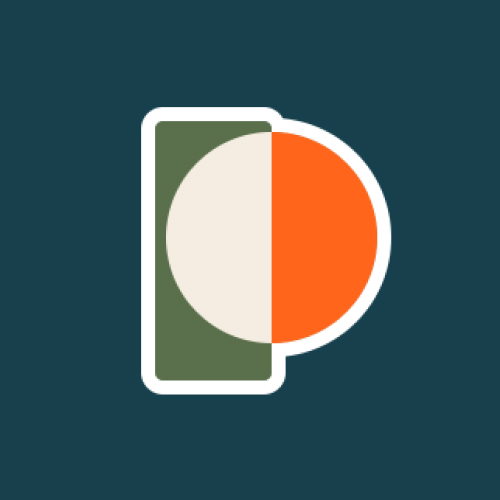
Making CAD education accessible to anyone, anywhere.
We hope you’ve been enjoying the wealth of free Fusion training provided by Product Design Online. Our commitment to empowering individuals like you with valuable skills is at the core of what we do.
If you’ve found our free content beneficial in your learning journey, we kindly ask for your support through a donation. Your contribution will not only help sustain the availability of free materials but also enable us to expand our offerings and reach even more learners globally.
Please select a donation method
Transcript
Welcome to Day #14 of Learn Fusion 360 in 30 Days. I’m Kevin Kennedy,
and today we’ll model this flathead screwdriver. We’ll discuss the 3-point arc command, making the size adaptable, and more!
We’ll start with the handle of the screwdriver as one component, followed by the shank as a second component. When planning, you’ll find it helpful to create all known components upfront.
Let’s create two new components, making sure we follow rule #2 and rename them respectively. The first one will be named “Handle,” while the second one will be named “Shank”.
Let’s activate the Handle component and start designing the basic shape of the handle by drawing a center circle on the XZ origin plane. Remember, we can use the shortcut letter C to activate it, followed by selecting the plane. I’m choosing this plane as we’ll draw the screwdriver as if it were lying on a table.
We can then Extrude this to a distance of 100mm.
Don’t forget to Save your Design File if you haven’t already. Remember that Fusion 360 saves files to the cloud, which means you’ll always want to save the file right away, followed by saving ‘versions’ as you design key parts of your design.
Let’s now add some groves to our handle to help with grip.
We’ll start sketching on the back side of the cylinder. Once again, use a center circle.
This time, I’ll start the center circle on the edge of the existing cylinder. Make the diameter 6mm and double-check that the center of the circle is snapped to the edge.
We’ll then apply a horizontal constraint to force this circle to remain horizontal with the origin point.
With Extrude active, select the right half of the circle, and drag the arrow into the existing 3D body to cut away material. Let’s remove 75mm.
This represents the first groove. To keep our sketches simple and manageable, we’re going to create the rest using modeling features instead of sketches. This is typically best practice.
Activate the solid modeling circular pattern feature. Make sure you activate it from the Solid menu and not the Sketch menu.
Select “features” as the pattern type, which allows us to select the extrude feature in our parametric timeline.
We’ll then use the axis selector to define the Y axis in the Browser. Keep in mind that we started our original sketch at the center of the origin. This allowed us to leverage the existing origin planes and axis. However, we could also always create an additional axis from the construction menu if needed.
We want the pattern to appear symmetrical around the cylinder, so I’ll leave the Disbituion set to ‘Full.’
For the quantity, I’m going to use 6. However, feel free to experiment with this and choose several instances that you like.
The compute type offers 3 different ways that Fusion 360 calculates patterns. For small models like this screwdriver, we’ll leave this set to the default of Adjust. Note that you can use the other two options when your computer or Fusion 360 cannot handle computing more complex patterns.
We’re going to round over the sharp edges in a minute, but let’s first add a divet at the front, where our thumb and forefinger will rest.
Start with a sketch on the YZ origin plane, as it splits the model down the middle. We’ll sketch the side profile, which will allow us to revolve it around the model, cutting it out from the existing cylinder.
We’ll need to use Project or Intersect any time we need to reference existing geometry. In our case, our sketch plane intersects the edge that we need to reference. We can use the “Intersect” command.
Select the 3D body and notice the top and bottom edges are now available for us to reference, as noted by the purple geometry.
We’ll now activate the 3-point arc command.
We’ll add dimensions after placing the arc. Start by selecting two points on the projected line, followed by placing the radius of the arc.
With the Sketch dimension tool, define the radius as 13mm.
We’ll also define the distance from the front edge to the first arc point, making this 3mm.
Notice our arc is still not fully-defined, as the sketch point is white. We need to add one final dimension to the center point of the arc and the front edge. This will be 9mm and will prevent the arc from moving around.
In the Solid tab, we’ll activate the Revolve tool. The profile is already selected for us. Define the axis as the Y-axis. This will default to a cut operation, so we can click OK.
Throughout the design process, there will be many times that you’ll need to punch in dimensions without knowing them. The wonderful part of parametric design is that we can simply edit our sketches or features to change the dimensions as desired.
I’d like to make this arc a bit more shallow. I’ll change the radius to 14mm, and the distance to the center point to 11mm.
Before we add our Fillets, let’s add the center hole for the shank. It’s important to note that you want to add Fillets and Chamfers at the end of your component’s timeline, when possible. This will make design changes easier later on, as Fillets often cause downstream errors by affecting sharp edges that you may have referenced.
Create a new sketch on the front face of the cylinder. Make this center circle 7mm in diameter. We’ll then extrude it to a depth of 50mm.
After completing this, take a minute to rename all of your sketches. I encourage you to get into the habit of this. Make the names descriptive of the task they include. Find a naming convention that works for you or your team and stick with it.
Let’s now activate the Fillet command to apply the desired rounded edges.
Start by selecting the two edges of our divet. This radius will be 5mm.
Add a new selection set, and select the front edge of the screwdriver. This will be 1.5mm.
Add a third selection set, this time selecting the back 6 edges of the handle. Once selected, we’ll define this as 10mm, which leaves this with a large rounded end.
Let’s click OK to save these Fillets. At times, you’ll find it best to break many fillet selections into two different Fillet commands. This can often help the fillets compute better while also making them more manageable.
Let’s add two additional fillets, starting with a 2mm fillet to all of the long edges of the handle. Once those are all selected, we’ll add a new selection set and select the two short edges for all 6 grooves.
Once selected, we’ll set this to 1mm and click OK.
We’re now ready to start designing the shank of the screwdriver. Remember we’ve already created the component. We simply need to activate it before doing any design work.
To create the shank, we’re going to start with a new sketch on the inner surface of our hole cutout.
This can be hard to select so we can use the following selection trick.
Left-click and hold over the area where we see the desired face. This will present us with a list where we can cycle through the faces until we find the correct one. Once the correct face is highlighted, right-click anywhere in the Canvas and select “Create Sketch.”
As you design your 3D models you should always be considering your design intent – or how you want the model to be adaptable.
In this example, I’d like to design this screwdriver so I can update the diameter of the shank by simply changing the sketch for the hole cutout. With that in mind, we’ll want to use the Project command to project the existing edge into our current sketch.
This means that our sketch is driven by the existing geometry. We don’t need to apply any sketch constraints or dimensions. We’ll test this in a minute.
Let’s first Extrude this to a distance of 150mm. Remember to use that selection trick if needed.
Let’s now test the design. I recommend testing your design per the design intent as you go. Waiting until the end puts you at risk to have to fix things, or even worse, remodel areas from scratch.
Let’s edit the “Shank Diameter” sketch. For exaggeration, I’ll update this to 15mm.
Once we finish the sketch, our Shank updates accordingly, without us having to do anything. Again, because we projected the geometry, our shank will always adapt to the size of the hole.
I’ll go ahead and revert this to the original dimensions.
Let’s finish up the design with the screwdriver tip.
If we want to reuse our design and simply design various tips, we could create a new component for the Tip. Be cautious when creating new components and make sure you create them from the topmost level unless you want them to be nested.
Select the front face of the shank and Extrude this to a dimension of 10mm.
It’s important to note that this concept of referencing existing faces is helpful for small or quick tasks. However, you should use sketches and projected geometry when working on more complex models. The downside is that we have an Extrude in our timeline, but no sketch to alter if needed. That’s okay in this case, as I don’t plan on changing the circular shape of the tip.
Start a new sketch on the YZ origin plane.
Again, we’ll need to use the Intersect tool to project the existing edges to our active sketch plane.
This will allow us to sketch a 3-point arc that touches the front edge and the top edge. Place it without defining any dimensions.
Notice how the first endpoint can still move around. We’ll apply a vertical constraint to this endpoint and the corner point above. This will ensure it stays on this line.
Let’s add a sketch dimension between this first endpoint and the center point. We’ll make this 0.5mm.
We can also define the dimension between the corner edge and the second endpoint. Let’s make this 9mm.
Lastly, add a 16mm radius dimension to the arc.
We’ll need to close our sketch profile on the front with the Line command. Once complete, activate the Extrude command.
We’ll make this a cut operation that follows the Symmetric Direction. The Extent Type will be “All” so it cuts away all of the existing 3D body.
We can now complete the tip by mirroring the extrude cut feature to the other side.
Activate the Solid modeling mirror command. Use the Features type and select our last Extrude. We’ll use the XY origin plane as the Mirror plane.
Our tip and screwdriver are now complete.
This model is a fun one to experiment with using Fusion 360’s appearances.
[Upbeat Music]
You’ve successfully completed the screwdriver. I’ll see you on Day #15 as we 3D model a painter’s tripod.
[End Upbeat Music]