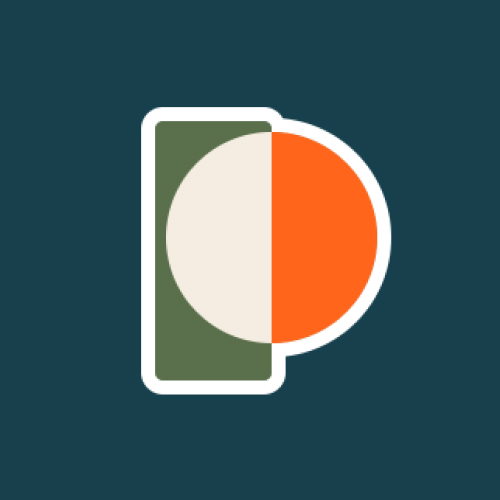
Making CAD education accessible to anyone, anywhere.
We hope you’ve been enjoying the wealth of free Fusion training provided by Product Design Online. Our commitment to empowering individuals like you with valuable skills is at the core of what we do.
If you’ve found our free content beneficial in your learning journey, we kindly ask for your support through a donation. Your contribution will not only help sustain the availability of free materials but also enable us to expand our offerings and reach even more learners globally.
Please select a donation method
Pattern Compute Types
When the (solid modeling) pattern Type is set to Features, select a Compute Type:
- Optimized: Creates identical copies by patterning feature faces. (Fastest)
- Identical: Creates identical copies by replicating results of original features. Use when Optimized is not possible.
- Adjust: Creates potentially different copies by patterning features and calculating the extents or terminations of each instance individually. (Slowest)
Tip: Try selecting another compute type if it’s producing funky or undesirable results. For large or complex patterns, suppress them when not in use. This will help with load times, reducing any experienced latency with Fusion 360.
Transcript
Welcome to Day #15 of Learn Fusion 360 in 30 Days. I’m Kevin Kennedy,
and today we’ll model this painter’s tripod, which is a fun and practical 3D print. We’ll discuss lofting to a point, circular patterns, copying components, and more.
I’ve gone ahead and created a component for the first tripod. This will be critical once we complete the design and want to create copies.
We’ll start by sketching the bottom contour using the Line command. Activate the Line command with the shortcut letter “L” and select the bottom origin plane.
At times, you’ll find it easiest to quickly create your sketch geometry, followed by adding constraints and dimensions.
Sketch out a triangle shape, starting from the origin point. Just be sure that it’s fully closed, as signified by the blue background highlight.
We’ll want to add the equal constraint to all three sides of the triangle. This will allow us to add a single sketch dimension that drives all three lines.
Remember, this is the best practice in parametric design. You don’t want to manually add the same dimension to all three sides.
I’ll add a sketch dimension of 60mm to any of the three sides.
Notice our three lines are now all 60mm. We can verify this by selecting them individually to look at the dimension in the lower right corner.
We’ll also double-check that our sketch is fully defined, with the red lock icon in the Browser. Don’t forget to rename your sketch as well.
To Loft to a point, we’ll need to sketch above this existing sketch.
We’ll use an Offset construction plane. This will provide the area to sketch on.
Select the bottom origin plane as the plane to offset from, then type our desired distance of 50mm.
One important note with the construction planes. These are technically infinite and the orange plane is for visual reference only. If needed, you can drag the corners or edges to resize them. This is never required but can help you when you’re trying to visualize what the planes intersect.
Let’s right-click on our construction plane and select “Create Sketch.”
To ensure our model is parametric for future changes, we’ll need to create our sketch point by referencing the existing triangle, ensuring it stays in the middle.
Remember we can use the Project command and select our three existing line segments. This will project the three lines into our existing sketch while pulling in any future changes.
We will draw 2 construction lines from the vertex of the triangle to the opposite midpoint, giving us the exact centroid, or the centerpoint of the triangle.
Once those are complete, I’ll select the point feature from the sketch dropdown menu, and I’ll select where it snaps where the two construction lines intersect.
Before we create the Loft, let’s double-check that our geometry is set up correctly.
If we edit the original sketch, we can change the sketch dimension, and our top point and the projected triangle should adapt accordingly. For example, I’ll make this 100mm.
Notice how the sketch point remains in the middle as the Projected geometry is driven from the original sketch.
This concept of projecting geometry is critical in making your models fully parametric.
I’ll revert the size changes back to 60mm.
Let’s now activate the Solid modeling Loft command.
During the complex glass bottle lesson, on day 4, we looked at lofting with four different closed profiles. The Loft command also allows you to loft to a sketch point instead of a closed profile.
Select the bottom sketch profile, then select the sketch point. We now have our basic pyramid shape.
Because we’re planning to 3D print this, we’ll use the Shell command to hollow out the pyramid.
With Shell active, select the bottom surface and define the thickness as 2.5mm.
We may also want to cut some circles out of the sides to reduce the materials further.
Right-click on any one of the three faces and create a new sketch.
Once again we’ll want to project the existing geometry to ensure our circle adapts to any size changes.
This time, I’ll select the middle of the triangle which will automatically reference the outer contour – or the three lines that make up the triangle.
Similar to before, we’ll create two construction lines that help us find the center point.
However, this time we’ll use the Center-Circle command instead of creating a sketch point.
Define the circle’s diameter as 25mm.
With the Extrude command active, we can select our circle profile and cut away the existing material.
We’ll leverage the “To Object” Extent type and select our inner face to ensure this cuts up to the inner face, even if we decide to change our Shell thickness.
We’ll now leverage the Circular Pattern feature to get the circle on the other two sides. It’s important to remember that Circular Pattern exists in both the Sketch environment and the Solid modeling environment. Be sure to activate the Solid Modeling feature.
For the “Object Type,” we’ll choose the features option. This allows us to select the Extrude feature in the timeline.
For the Axis, we can’t leverage the Z axis as it’s off to the side. This is a great scenario where we could leverage the construction axis, similar to construction planes.
I’ll cancel the Circular Pattern feature and activate the feature called “Axis Perpendicular to Face at Point”. This one will work in our scenario as we can select the bottom planar face, followed by the topmost point of the pyramid. Which plane or axis you choose will always depend on the existing geometry that’s available to reference.
Notice this creates an axis running through the middle.
Let’s re-activate Circular Pattern, this time completing it with our new axis.
The quantity should be set to 3.
You may also find that the Adjust compute type leaves us with a funky result. I’ve placed some notes about these different computing types on the resource page. Just note that with the pattern tools, you may need to select a different computing type to get the desired results.
We now have the circles on all three sides.
Lastly, add a 1-2mm Fillet to the top three edges of the pyramid.
Let’s now take a look at leveraging our component to create copies.
Right-click on the Component in the Browser to select Copy. Note that you can also use CMD + C on Mac or CTRL + C on Windows.
We can then right-click on the top-level assembly to paste the component. However, it’s important to note there is a Paste feature and a Paste New feature.
Let’s start with the Paste option.
After selecting Paste, move the copy to the right with the position manipulators.
Pasted components will always remain an exact replica of the original. They’ll also inherit any design changes.
Contrary, Paste New means the copied component will no longer inherit any changes. This means we can leverage Paste New to create additional sizes or modifications without affecting the others.
I’ll right-click again this time using Paste New.
Notice the Pasted New component has a different naming convention. I recommend renaming this as well as the numbers can quickly become confusing.
Let’s activate the component and edit the original sketch.
I’ll make this one 100mm.
We can also edit our height by updating the dimension of the offset construction plane to 90mm.
Lastly, let’s update the circle sketch to have a diameter of 50mm.
Notice how quickly we were able to create a newly sized part, without starting again from scratch. You can take this even further by leveraging equations and user parameters to automatically adjust dimensions throughout your design.
You may also find it helpful to leverage components with the Pattern command when setting up multiple copies for 3D printing or other use cases. For example, we could leverage the Component object type with the Rectangular Pattern tool. This will allow us to create as many duplicates as desired.
We could then leverage the Joint command to precisely position them.
Components also allow you to copy and paste objects into other design files. Because they group relevant sketches, bodies, construction objects, and so on, we can continue to make updates to our dimensions at any time. Components are key when maintaining the full parametric integrity of the part.
[Upbeat Music]
You’ve successfully completed the Painters Tripod. I’ll see you on Day #16 where we’ll discuss all of the sketch constraints in greater detail!
[End Upbeat Music]