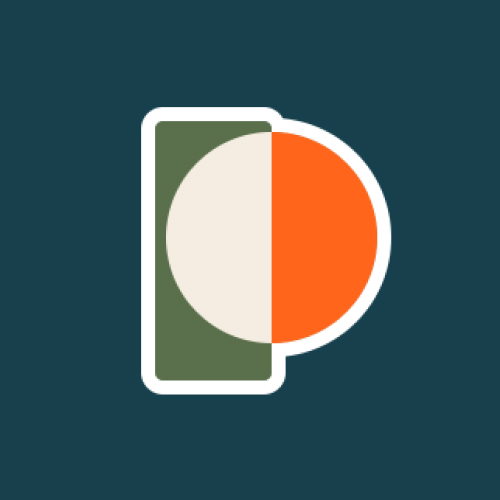
Making CAD education accessible to anyone, anywhere.
We hope you’ve been enjoying the wealth of free Fusion training provided by Product Design Online. Our commitment to empowering individuals like you with valuable skills is at the core of what we do.
If you’ve found our free content beneficial in your learning journey, we kindly ask for your support through a donation. Your contribution will not only help sustain the availability of free materials but also enable us to expand our offerings and reach even more learners globally.
Please select a donation method
Autodesk Instructables: ‘Make it Move’ Design & Make student challenge
Special thanks to Autodesk for sponsoring this video! Kevin will be a guest just for the 2024 ‘Make it Move’ challenge, hosted by Instructables (Autodesk).
Contest rules and entry: https://www.instructables.com/contest/makeitmove2024/
Motion Study Demo Files
Use the Autodesk Fusion files below
- Automata – https://a360.co/3ZNXUsE
- Trammel of Archimedes – https://a360.co/4enTHQR
- Tripod – https://a360.co/3BsrucY
Select the Fusion ‘share link‘ above > select the ‘Open in Fusion’ button > select ‘Open’ when prompted. This will open the demo file in your Autodesk Fusion application. Everything is set up and ready to use with the tutorial.
Key Terminology for Motion Study in Autodesk Fusion
- Motion Study: A kinematic simulation feature in Autodesk Fusion used to analyze the movement of components based on predefined joints, without accounting for physical forces like gravity or friction.
- Joints: Connections between components that define their allowed relative motion, such as revolute (rotation) or slider (linear) joints.
- Degrees of Freedom (DOF): The number of independent movements a component or assembly can have, such as translation or rotation along specific axes.
- Action: A point on the timeline that marks a specific position, orientation, or motion of a component at a defined time.
- Joint Limits: Constraints applied to joints that restrict the range of motion, defining minimum and maximum values for movement.
- Component Motion: The movement of parts in the model as defined by the joints and keyframes along the timeline.
- Playback Controls: Tools to play, pause, rewind, or loop the motion sequence for real-time review of component movement.
- Looping (Infinite): A setting that allows the kinematic motion sequence to continuously repeat from start to finish
Transcript
Whenever you set up Joints in Fusion, you probably drag the model around to check if they’re working. But it’s often tricky to tell if everything’s functioning correctly.
Today, I’ll show you an often-overlooked feature that simulates and analyzes the movement of assembly components: Motion Study.
Motion studies allow you to perform kinematic motion analysis based on the model’s Joints. This is particularly useful for detecting collisions, testing mechanical functions, or optimizing designs for movement.
For this first example, I’ve already applied a Revolute Joint to the handle. The handle is connected to the center rod with a Rigid Joint, so when the handle moves, the rest of the design should follow.
To test this, we’ll select the Revolute Joint for the handle. After selection, we get a “curve line” that represents the joint’s motion. This line lets us add points that define how the joint moves along the timeline.
Let’s add a point anywhere on the curve. Because we’re working with a Revolute Joint, we can set the angle of rotation. If we want the handle to rotate a full 360 degrees, we simply enter 360 as the angle.
We now have to consider where this action should take place on the motion curve, which ranges from 0 to 100. Since we want a full rotation over the entire motion, we’ll set the step to 100, placing it at the end of the curve.
Once that’s done, we can play back the motion to see it in action!
You’ll notice we can adjust the speed to make it move slower or faster.
I’ll slow this one down to the lowest setting to make it easier to see.
By default, the motion plays through once, but you can loop it infinitely or have it play back and forth, depending on your project needs. I’ll set this one to loop infinitely.
Looking at the design, you’ll see that the far-right disc isn’t moving properly. It seems like I forgot to apply the Tangent Relationship between the disc and the dowel, which is why it’s not functioning correctly.
Let’s save this motion study by clicking OK, so we can fix the issue. In the Assemble dropdown, we’ll select Tangent Relationship. For the first component, I’ll select the outer edge of the disc, and for the second, the bottom of the dowel.
Now that we’ve fixed that, let’s go back to our Motion Study in the Fusion Browser, right-click on it, and select Edit. We’ll play it back to make sure everything is working now.
With the Tangent Relationship fixed, we can see that the entire motion is working smoothly, and all the joints are behaving as they should.
Before we continue with more examples and common pitfalls, I’d like to thank Autodesk for sponsoring this video.
Autodesk is hosting the Make it Move Design & Make Student Contest on Instructables (with prizes), inspiring students to create projects that incorporate motion. Whether it’s a robot, gadget, kinetic sculpture, or even something simple like a wind chime—if it moves, it qualifies.
To participate, you must be a student enrolled in high school or a post-secondary institution. The goal is to design something that not only works well but also brings joy or solves a problem.
If you’re not eligible, be sure to share the contest link with any students you know who might be interested. It’s a great opportunity for them to showcase their creativity and skills, as well as win prizes!
Let’s now look at a common issue you might encounter. I have this Trammel demo file set up just like the previous example. However, you’ll notice the motion glitches as it loops.
The problem is the Revolute Joint starts at negative 37 degrees instead of 0 degrees, which causes the loop to be jerky.
To fix this, we need to adjust the Motion Limits. Right-click on the Revolute Joint in the Browser and select Edit Motion Limits. Turn on the Rest Position option, which lets you define where the joint should rest when it’s not moving. Set this to 0 degrees.
Next, we’ll need to click Revert in the toolbar to move the joint to the rest position.
Because our original motion study remembers the previous placement, we’ll delete the existing motion study and create a new one.
With the new study, the trammel now loops smoothly without any glitches.
Now, let’s explore how to apply multiple motion curves in a motion study using this tripod model.
We’ll start by collapsing the legs. First, I’ll select the three slider joints that control the legs. You’ll see each joint listed on the right, where we can toggle visibility or remove them if needed.
For one leg, I’ll add a point on the motion curve, defining a 50mm slide inward and setting the step at 20. If the leg doesn’t move, we might need to reverse the direction by adding a minus sign.
I’ll repeat this process for the other two legs and playback the motion to check that everything moves smoothly.
I’ll now select each of the three Revolute joints on the model. Let’s define the step at 40mm, so the legs close together after the lower legs slide inside.
If you happen to click on the curve by accident, you can always remove a point by selecting the Remove icon.
Based on the joint limits, I know the legs should be straight when they reach 20 degrees.
Remember to add a negative sign if the rotation is in the wrong direction. We’ll repeat this for the remaining two Revolute Joints.
Once everything is set, use the “back and forth” playback to check the motion.
You can always adjust the timing by changing the steps, which will affect the overall motion.
For example, we could shift all revolute actions to step 100 and see how that alters the sequence.
You could also stagger the steps so one leg collapses at a time.
Before wrapping up, let’s quickly address a few common questions about Motion Studies.
The first is “How to save a video of the motion study”
Unfortunately, Fusion doesn’t have a built-in option to export a video. You’ll need to screen-record the study while it plays back.
Second, you can share motion studies with others by simply sharing the design file. The motion studies are saved with the file as long as you click OK and not Cancel.
To summarize, Motion Studies in Fusion are perfect for simulating basic kinematic movement, whether you’re working with rigid bodies, slider or revolute joints, or even mechanical motions like gears or linkages.
Just remember that this tool focuses on kinematic movement, not real-world physics. For that, you’ll need to use Fusion’s Simulation workspace.
[Upbeat music]
If you enjoyed this lesson, be sure to check out my video on Fusion’s Animation Workspace.
[End upbeat music]