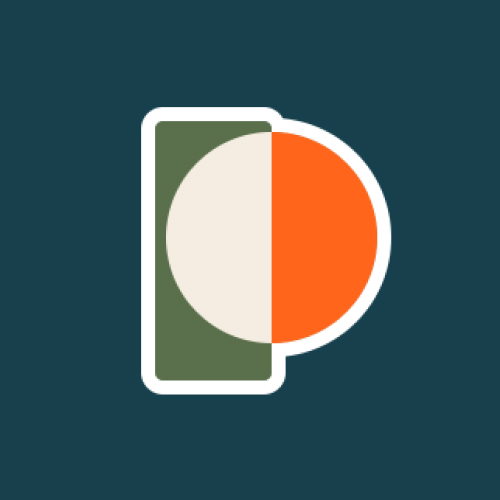
Making CAD education accessible to anyone, anywhere.
We hope you’ve been enjoying the wealth of free Fusion training provided by Product Design Online. Our commitment to empowering individuals like you with valuable skills is at the core of what we do.
If you’ve found our free content beneficial in your learning journey, we kindly ask for your support through a donation. Your contribution will not only help sustain the availability of free materials but also enable us to expand our offerings and reach even more learners globally.
Please select a donation method
Transcript
Welcome to Day #20 of Learn Fusion 360 in 30 Days. I’m Kevin Kennedy,
and today we’ll add 3D printable hinges to our parametric box created on Day #19.
Let’s start by deleting our Joint command in the parametric timeline. This will allow us to reposition the top box so the lid is flat as if it were on the 3D printer’s build platform.
Select the Joint command in the timeline and press the Delete key, or right-click and select Delete. You can delete timeline features at any time. However, it’s important to keep in mind that you may affect downstream features if there are any sketches or items that come after the deleted feature.
Activate the Joint Command in the Toolbar at the top.
Let’s first hide the Bottom Box in the Browser, ensuring we only select the Top Box component.
We’ll select the top right corner for the first Joint Origin.
For the second Joint Origin, we’ll select the corner on the opposite side of the Bottom Box.
Our goal is to have the boxes side by side with the Joint. However, we’re going to use the offset field to make them exactly 9mm apart. This will leave a large enough gap for the hinges.
We’re going to make the hinges as small as possible for easy 3D prints, so let’s edit our user parameters and make this test box 30mm for the width and 20mm for the height.
Our offset should still be 9mm between the two boxes. We can quickly check this by Shift-clicking the two edges, and you’ll notice they’re still 9mm apart. This is one advantage to placing them with the Joint command instead of the Move command. We can change our box size without affecting the 9mm gap.
We’ll now activate the Box Bottom component. Remember this is critical in ensuring our sketches and other assets are correctly grouped.
Start with a new sketch on the side of the box. It doesn’t matter which of the outer sides as we’re going to eventually mirror the hinge to create the other half.
We’ll start with the side profile of the hinge design. We plan to make two simple flanges. One will have a nub that sits within a cavity on the other flange.
I’ll first draw a 4.5mm horizontal line starting at the top corner. Make sure it snaps horizontally or manually apply the Horizontal constraint.
We’ll then create an 8mm Center Circle on the endpoint of the line. Notice this leaves a 0.5mm gap on each side, which is why we made our Joint offset 9mm.
Lastly, we need an angled line that connects the box to the bottom of the circle. Start the line at the bottom corner of the box. Then, you’ll want to find the point on the circle where it automatically adds a Tangent constraint.
The Sketch should now be fully defined.
Take a minute to rename your sketch in the Browser.
We’ll Extrude these two sketch profiles to a distance of 5mm. Remember to use the minus symbol if you need to flip the direction of the profile. We also want to set this to ‘New Body’ which will allow us to Mirror this specific body later.
The side of the hinge is now complete! We’ll create a new sketch on the inner side for the nub that will connect with the opposite flange.
To make sure we use the same center point, we’ll first use the Project command, activating it with the letter “P”. Select the outer line. Make sure “Projection Link” is checked, and select OK.
This leaves us with Projected geometry, including our circle’s center point.
We’ll start a center circle off the same center point, knowing we won’t lose the reference if we change the size of the hinge’s circle.
This circle will be 4mm.
We’ll Extrude this to 3.8mm, which makes sure it doesn’t stick past our inner hinge piece.
Adding a taper will also help the 3D-printed hinge move freely. You can experiment with this number, but I’ve found -10 to -14 to work well. We can also let this body join the existing hinge body.
Lastly, we’ll add a 1mm fillet to the outer edge. I’ve found this helps prevent this from sticking too much with the inner hinge.
Once complete, we’re ready to create the inner hinge. Start by activating the Box Top component.
We’ll create a new sketch on the inner side of the existing hinge.
Once again, we need to Project geometry to make sure we can reference it. Activate “Project” and select the profile.
Add a center circle starting from the projected center point. However, we’ll want to avoid adding unnecessary dimensions, so we’ll select the outer projected point.
Minimizing dimensions will help keep your parametric models adaptable.
We’ll also create a small horizontal line that connects the circle to the box. Apply a horizontal constraint to the line, if not automatic. You may also have to apply a coincident constraint to either endpoint of the line.
Next, draw a line that connects from the lower point of the box to the circle, making sure to connect with tangency.
Lastly, you’ll see that our lower profile is not yet closed. We’ll need to project the existing edge of our box.
Our sketch is now fully defined with only Projected geometry and sketch constraints. Everything will adapt if we make changes to the original.
Let’s activate the Extrude command so we can Extrude this flange to 5mm as well. We also need to change our ‘Start’ option to ‘Offset,’ allowing us to add a .6mm offset to the Extrude, providing a clearance between the two hinge pieces.
Once again, make sure that your Extrude is set to ‘New Body’.
We’ll need to cut out the nub from the inner hinge. We can do this using the Combine command.
With Combine active, we’ll select the Inner Hinge Body as our Target Body.
The Tool body will be the Outer Hinge Body, as it includes the nub.
With the Operation set to Cut, this gives us a red highlight of what will be removed.
Double-check that you have ‘Keep Tools’ checked as we do want to keep our outer hinge.
After selecting OK, we can hide the Bottom Box and check the outcome.
You’ll also want to add a 0.2mm to 0.8mm clearance to this inner cavity. This will ultimately depend on your slicer settings, 3D printer, and other factors. I recommend doing a test print with a 0.8mm clearance first, then work your way smaller.
You can also use the clearance to determine how ‘loose’ the hinge result is.
Activate “Offset Face” and select each face of the inner cavity. I’ll set this as -0.4mm, since this will apply all the way around, resulting in our desired 0.8mm starting clearance.
We’ve now completed the hinge and can Mirror this over to the other side.
We’ll need a plane directly in the middle of our box to ensure we have something to select for our mirror plane.
With our top-level component active, let’s create a Midplane construction plane. Midplanes allow us to select opposite faces of the box, resulting in a plane directly in the middle.
Activate the Mirror tool from the Create Menu of the Solid tab. Make sure you’re not in a Sketch tab as there is a separate sketch mirror tool.
We’ll want to do one body at a time, which will help the bodies end up in the respective components.
Select the first body, followed by our Midplane construction plane as the Mirror Plane. Once complete, let’s repeat this process for the other body.
Optionally, you can use the Combine tool to join the hinge pieces to their respective box.
Our 3D printable hinges are now ready for a test print!
You can export your file as an STL mesh file by right-clicking on the component in the Browser. Select Save as Mesh, then save the STL to your Desktop or send it directly to your Slicer.
I recommend printing with a 0.1mm layer resolution.
Let me know how yours turns out, especially if you print with some different clearances or sizes!
[Upbeat Music]
I’ll see you on Day #21 where we’ll take a look at creating a one-part mold.
[Upbeat Music]