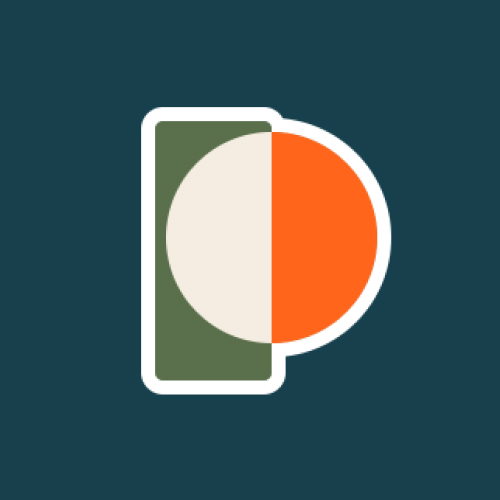
Making CAD education accessible to anyone, anywhere.
We hope you’ve been enjoying the wealth of free Fusion training provided by Product Design Online. Our commitment to empowering individuals like you with valuable skills is at the core of what we do.
If you’ve found our free content beneficial in your learning journey, we kindly ask for your support through a donation. Your contribution will not only help sustain the availability of free materials but also enable us to expand our offerings and reach even more learners globally.
Please select a donation method
Mold Release Products and Tips
Creating 3D Printed molds can be a fun and easy way to make duplicates, without having to 3D Print each object!
- In general, use a soft mold material (TPU) when casting a hard material (Resin, Plaster, etc) OR use a hard mold material (PLA Plastic) when casting a softer material (Smooth-On Vytaflex 30).
- I recommend many Smooth-on products which can be found at local distributors around the globe. They do also sell (select) Smooth-on products on Amazon, just be cautious of the prices as they tend to fluctuate more on there (from 3rd party sellers)
- Universal Mold Release is by far my favorite ‘mold release’ product.
- In a pinch, you can try using PAM, Olive Oil, or Vaseline – though results with these vary significantly based on the type of material you cast.
Transcript
Welcome to Day #21 of Learn Fusion 360 in 30 Days. I’m Kevin Kennedy,
and today we’ll create a simple one-part mold for 3D printing.
To start, let’s model a simple keychain that we’ll make a mold from, allowing you to print the mold for faster duplicates using resin or another material. I’ll also put some notes and links to some mold-release products that I recommend.
With a new component already created, we’ll start sketching out our keychain.
Let’s press the keyboard letter “R” to activate the Rectangle tool, and we’ll start sketching on the bottom origin plane.
Start the sketch at the center origin point. Make the length 50mm and the width 35mm.
We can then Extrude this to a height of 3mm. Note that these dimensions are not required, feel free to make any shape or size you would like.
I’d like to have the edges rounded over, so I’ll activate the Fillet command and select all four sides. Once selected, I’ll define the fillet radius as 7mm.
We also need to add the keyring hole.
Let’s right-click on the top surface and select Create Sketch.
Sketch a line starting from the midpoint of one of our ends. Remember to look for the triangle icon that represents the midpoint constraint.
We’ll make this 5mm in length. We can also make this a construction line as it’s for reference only.
Instead of sketching a circle and Extruding it, we can instead use the Hole command.
Activate the Hole feature and we’ll select the sketch point as the hole’s center point.
Instead of typing out the hole length, let’s set the “Extents” option as the “To” selection. This will allow us to select the bottom surface. We’re now able to update the thickness of our keychain and our hole will adapt automatically.
Let’s make sure our hole settings are set to “Simple,” “Simple,” and “Flat”.
The diameter can be set to your desired key ring size. 5mm is a good starting point.
We now have the basic keychain shape complete. Take a few minutes to customize it by using the Text command or by inserting an SVG file with a logo or other design.
Note that you may want to align the right side of the text box to just before the hole. This will allow you to space the text with the center alignment commands.
Lastly, Extrude your text or SVG design approximately 1 to 2mm. If the font you chose does not Extrude, you will have to right-click on the text and ‘Explode’ the text. This converts the custom font to spline geometry and will allow you to Extrude it.
Now that we have a simple keychain design, we can create a box for the mold as well as discuss the Draft command.
Let’s create a second component from our Browser. This one will be named ‘One-Part Mold’.
We’ll start with a new sketch on the XY origin plane. Whenever you’re working with components, make sure to use the correct origin planes that are nested under the component.
You may find it easiest to right-click on the origin plane in the Browser, followed by Create Sketch.
We’ll use the ‘Project’ command to reference the existing edge of our keychain. Using the body option will provide us with all of the outer geometry.
Now that it’s projected, as shown with the purple geometry, we can use the Offset sketch tool to create a 5mm offset. This dimension simply needs to be a few millimeters larger to encompass the design.
Let’s Extrude all of our sketch profiles 2mm past our 4mm total thickness. This should leave us with sufficient thickness to print the design.
Currently, our keychain and mold are taking up the same space. We’ll use the Combine command to cut away the keychain from the mold.
With the Combine tool active, select the mold body as the “Target Body”.
We’ll then select the Keychain body as the tool body. Change the operation to “Cut” since we want to remove the keychain from the mold body. We’ll also check ‘Keep tools’ to keep the keychain component.
Once complete, we have our basic keychain mold. However, we still have the most important part to complete, which is adding a draft angle to the mold.
A draft angle is a taper applied to the vertical walls of the molded component to assist with releasing the part from the mold.
In Fusion 360 this can be done with the Draft tool as well as the Chamfer tool. We’ve already applied Chamfers throughout this course, so let’s take a look at the Draft tool from the Modify menu.
Notice we have two different “types” to choose from. We’ll use the default of “Fixed planes.”
We then have to set the “Pull Direction,” which is the direction the object will exit the mold.
We can select either the origin plane or one of the planar faces on top of the model. After making a selection, an arrow appears representing the pull direction. You’ll want to confirm this is going in the right direction. If not, we can select the arrow to flip it.
Second, we need to define the Faces that will receive the Draft angle. This typically includes the main outer wall of the design, as well as any inner details, such as our keyhole and letters.
However, because the letters are only 1mm thick, you may be able to get away without a draft angle, depending on the material.
If you do apply a draft angle to the letters, I recommend doing it as a second Draft in your timeline, which will make it easier to adjust the letters and other features independently.
We’ll define the draft angle as 5 degrees. Between 1-2 degrees is often used for injection molded parts. However, the textured finish of FFF 3D printing is better suited for a 4 or 5-degree draft angle.
Double-check your angle is also pointing outward, allowing the object to release. If not, add the minus symbol in front of your value.
The keychain mold is now ready to print! To export your design for 3D printing, right-click on the Component in the Browser and select “Save as Mesh.”
Choose your preferred file type from STL or 3MF and save it to your local computer.
[Upbeat Music]
I’ll see you on Day #22 where we’ll take a look at creating a more complex two-part mold.
[Upbeat Music]