Ordering Sheet Metal
The following two places I recommend if you would like to order this napkin holder design (or any other sheet metal design you create!). I order from both of these regularly due to material type/bending capabilities.
- SendCutSend (Has more material choices overall, but is limited on bending capabilities)
- Fabworks (less material choices, but able to bend more complex designs)
Both have good powder-coating add-on services and they are comparable in pricing. However, it doesn’t hurt to upload your design to both to compare pricing before placing your order.
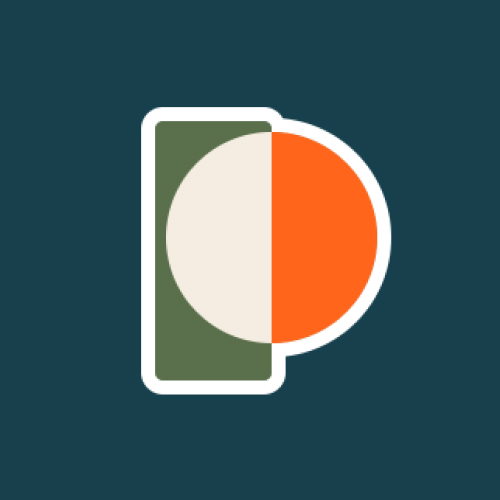
Making CAD education accessible to anyone, anywhere.
We hope you’ve been enjoying the wealth of free Fusion training provided by Product Design Online. Our commitment to empowering individuals like you with valuable skills is at the core of what we do.
If you’ve found our free content beneficial in your learning journey, we kindly ask for your support through a donation. Your contribution will not only help sustain the availability of free materials but also enable us to expand our offerings and reach even more learners globally.
Please select a donation method
Height Datum – Autodesk Fusion
In Autodesk Fusion’s Sheet Metal environment, the “Height Datum” refers to the reference plane from which the height of a flange is measured. When creating a flange using the Flange tool, you can specify the height datum to define where the height measurement starts from.
This can be particularly useful when you have multiple reference planes or faces in your design and you want the flange height to be consistent with a specific plane or face.
By selecting the appropriate height datum, you ensure that the flange height is consistent with your design requirements and measurements. It allows you to control the position and orientation of the flange relative to other features in your sheet metal design.
- Inner Faces: Measures the flange height from the intersection of the inner faces of the base flange and the new flange.
- Outer Faces: Measures the flange height from the intersection of the outer faces of the base flange and the new flange.
- Tangent To Bend: Measures the flange height tangent to the bend between the base flange and the new flange, parallel to the new flange.
Bend Position – Autodesk Fusion
In Autodesk Fusion’s Sheet Metal environment, the “bend position” refers to the location along the edge of a sheet metal part where a bend will be applied using the flange tool. It determines the distance from the starting point of the edge where the bending action begins.
When you’re using the Flange tool in Autodesk Fusion’s Sheet Metal environment, you typically start by selecting an edge or a chain of edges where you want to add a flange. After selecting the edge, you’ll specify various parameters including the bend angle, bend radius, and bend position.
The bend position is crucial because it determines the distance from the start of the selected edge where the bending process initiates.
Adjusting the bend position allows you to control precisely where the bend occurs along the edge, which is important for achieving the desired geometry and ensuring the proper fit and function of the sheet metal part.
- Inside: will position the bend inside the boundary of the outermost faces of the base flange and new flange.
- Outside: will position the bend outside the boundary of the innermost faces of the base flange and new flange.
- Adjacent: will position the bend so that it starts at the selected edge on the base flange.
- Tangent: will position the bend so that it is tangent to the selected edge on the base flange.
Transcript
Welcome to Day #24 of Learn Fusion 360 in 30 Days. I’m Kevin Kennedy,
and today we’ll look at the core workflow and basics of sheet metal design in Autodesk Fusion. You can use this workflow to design common household goods, such as this paper towel holder, bookends, napkin holders, and more.
It’s important to note that Fusion’s sheet metal tools may also be used for cardboard packaging and other design scenarios where creating a flat pattern is desired.
We’ll start with a New Component from the toolbar. At this point in the course, we’ve only created Standard Components.
When designing for Sheet Metal, you’ll want to change the component type to a Sheet Metal Component. After selecting “Sheet Metal,” you’ll find we now have a Sheet Metal Rule at the bottom of the dialog.
Sheet metal rules describe sheet metal material characteristics and how the parts are manufactured. For example, rules will dictate material thickness, bend radius, and corner relief. We’ll take a closer look at these rules later in this lesson.
For now, we’ll set this rule to the “Steel” millimeters option.
We’ll name this component ‘Napkin Holder’ before selecting OK.
All of the Sheet Metal tools are organized in the Sheet Metal tab. Within the Sheet Metal tab, you’ll find the Flange tool, which is the most used of them all. It’s common for sheet metal parts to start with a base flange, as it represents starting with a stock piece of metal.
Fusion’s sheet metal tools are parametric, just like the Solid modeling tools. Many of our sheet metal parts will start with a profile sketch for our base shape.
Let’s sketch a simple rectangle.
Press the keyboard letter “R” for the rectangle, and select the bottom origin plane to sketch on. This design will be symmetrical, so let’s switch to the center rectangle before selecting the origin point. This will make it easier to constrain things and keep it symmetrical.
We’re going to sketch the base of the Napkin holder, which has a length of 125mm and a width of 60mm.
After clicking to place the sketch, we’ll switch back to the Sheet Metal tab and activate the Flange tool. The flange tool helps us turn sketches into sheet metal faces.
To create a Flange, select the profile sketch and notice it automatically applies the sheet metal thickness based on the Steel rule we selected when creating the component. We’ll later discuss how we can change this rule.
When necessary, you can also choose which side of the sketch the flange sits on.
Let’s select OK.
At a glance, this result may look similar to a sketch with an Extrude. However, you’ll find that we have a sheet metal body in the Browser instead of a solid body.
Let’s take a look at the advantages of sheet metal flanges.
We now want to create the top two flanges of our Napkin holder. We’ll activate the Flange tool again, this time selecting the top of the two long edges.
We can then pull the blue directional arrow up to create these flanges. This is one of the great benefits of using the Flange tool. We can quickly create edge flanges from existing base flanges.
Let’s set the height as 130mm.
Within each of our edge selections, you’ll find that we can choose from different “Flange Width Types” if we don’t want our flange to run the entire length.
We can also define the angle if we need an angle other than 90 degrees.
Lastly, we can set our Height Datum and Bend Position.
The Height Datum controls where our flange height is measured. For example, if our 130mm height needs to be from the bottom of the product to the very top, then we would set this as Outside Faces.
If we wanted our 130mm to be from the inside face of the base flange, then we would set this to the Inner Faces.
I’ve added notes on these options below this video.
Our Bend Position controls where the bend is positioned between our base flange and the new flange. In our scenario, this is the new flange on each side.
If we want to retain our 60mm dimension from the width of our base flange, we’ll want to set the bend position to the Outside option. Outside will make the inside face of our two side flanges align with the edge from our base flange, retaining that 60mm dimension.
To show you the difference, I’ll set this to the inside option and measure the results.
Notice the value is 55mm, 5mm shorter than our base flange’s dimension.
I’ll set this back to the Outside option as I do want to retain the 60mm value.
These options may not feel important for something as simple as the Napkin Holder, but they’re important to keep in mind for future projects.
Height Datum and Bend Position can have a significant impact on sheet metal parts that require precise measurements.
We’ll now add Fillets to our top flanges to create the rounded portion of the design.
Fusion’s sheet metal bodies can be modified with most of the standard solid modeling tools. This includes Fillet and Chamfer.
I want this design to retain the arc at the top even if we change the overall width of the holder. We can achieve this by using the ‘Full Round Fillet’ type in the Fillet dialog.
Start by selecting the top center face. We then need to select both the left and right side faces for each of the Side selectors. Note that you’ll need to hold the Command key on Mac or the Control key on Windows.
This results in a fillet that will remain tangent to both of our sides, even if we change the width or height of our design.
Let’s repeat this for the other side Flange by adding a ‘New Selection Set,’ followed by repeating the same process.
The basic shape of our napkin holder design is now complete.
Let’s take a look at creating flat patterns before we finalize some design details.
A flat pattern is the shape of the sheet metal part before it is formed. Flat patterns show bend lines and other details which can be turned into 2-dimensional drawings, or DXF files used for manufacturing.
Activate ‘Create Flat Pattern’ in the toolbar. We’re then prompted to select the stationary face. The stationary face is typically the Base Flange that the rest of our flanges are created from.
Once complete, you’ll find Fusion turns our 3-dimensional sheet metal body into a 2-dimensional flat pattern, including our bend lines, bend zones, and centerlines.
Note that we’re also placed in a contextual Flat Pattern environment. This is important because when in the Flat Pattern environment you can add features specific for manufacturing, such as tabs.
Features added in the Flat Pattern environment will not be reflected in the folded model.
When complete, we can select ‘Finish Flat Pattern.’
Our model is folded back to its 3-dimensional shape and a Flat Pattern node is created in the Browser.
You can switch between the folded state and the flat pattern state using the Activate Flat Pattern radio button.
Let’s now finish off our design by creating a slot down the middle.
Create a new sketch on the upper flange.
We’re going to create a slot that matches the outer shape, so we’ll use the Offset sketch tool.
Before we select the edges, let’s uncheck the ‘Chain Selection’ option. This will allow us to select the left edge, top, and right edge, without the bottom.
I’m going to offset this -55mm. This value can be anything based on how small or large you want the slot to be for the final design.
We’ll then use the line tool to close the bottom of the sketch profile. Use a combination of straight lines and constraints to fully define the sketch.
Notice the bottom line is not yet defined. I’ll add a coincident constraint to the bottom line and our origin. This fully defines our sketch.
We can now use the Extrude command to cut these two sketch profiles out of our existing sheet metal body. Set the Extent Type as ‘To Object’ before selecting the opposite side. Remember this will help our design remain parametric when the overall width or material thickness changes.
You’ll notice my final design has a small hole in the bottom flange. A small hole is often required if you plan to have the part powder-coated, as they need this hole to hang the part throughout the coating process.
Let’s sketch a 3mm circle on the bottom flange.
We can dimension it so it’s 25mm away from the center origin and apply a horizontal constraint to keep it centered to the origin.
When you Extrude cut the hole, don’t forget to use the ‘To Object’ Extent type again.
Let’s now look at changing our Sheet Metal Rule.
This design was laser cut, bent, and powder coated by Fabworks, in a 14 gauge steel, which is approximately 1.88mm or 0.074 inches.
In Fusion, we can open the Sheet Metal Rules feature to create a custom rule or select from existing rules.
Toggle the library open and select the ‘New Rule’ icon next to the Steel millimeters option.
This will create a new rule, starting with the characteristics of the existing rule. We can rename this specific to either our project or material thickness. For example, I’ll name this 1.88mm Steel. I’ll also add 1008, which is the type of steel.
Most importantly, we need to update our desired thickness, setting this to 1.88mm.
You will also find that each rule includes the K-factor and Bend and Corner conditions. Each of these items will vary based on the type of material, the type of bending, and other considerations. We won’t discuss the K-factor and these other details in this lesson but note that this is important to consider and will affect your final design.
I used a K-factor of .38 if you’d like to get your final design manufactured by Fabworks.
Now that our rule is in the library, let’s close the dialog and head to our Sheet Metal component in the Browser.
Each Sheet Metal component has a rule associated with it. Hover over the rule and select Switch Rule. Select the desired rule from the dropdown list.
Pay close attention to the thickness of the model as I select OK. You’ll notice the thickness changes based on the new sheet metal rule. The K-factor and other bend conditions will also affect the bend radius of the design.
It’s important to note that changing the Sheet Metal Rule can be done at any time. However, depending on the design, you may want to set the desired rule early in the design process, so you can account for different design elements accordingly. Especially when dealing with corner elements.
Changing the sheet metal rule will also affect the Flat Pattern if the thickness changes. Notice we have a warning icon in the Browser, next to our Flat Pattern. We can simply activate the Flat Pattern which will generate the latest flat pattern based on the existing design.
Now that our part is ready to be manufactured, we can export our flat pattern as a DXF file to send to the laser cutter. However, the file type ultimately depends on the manufacturer’s requirements. SendCutSend often requires a DXF file, while Fabworks now allows you to upload the design from a STEP file, meaning you no longer need to worry about the flat pattern.
In that case, we can right-click on the Sheet Metal component to select ‘Export.’ Choose the STEP file and export it to your local computer. You can then upload the file, choose materials and optional add-on services, and order your parts.
You’ve successfully completed a basic sheet metal design!
[Upbeat Music]
I’ll see you on Day #25 where we’ll take an introductory look at Autodesk Fusion’s Surface modeling tools.
[End Upbeat Music]