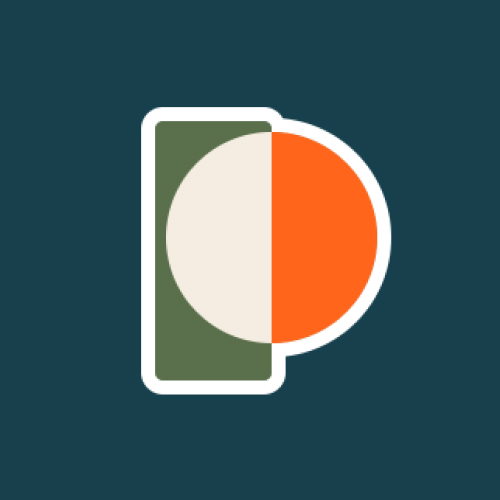
Making CAD education accessible to anyone, anywhere.
We hope you’ve been enjoying the wealth of free Fusion training provided by Product Design Online. Our commitment to empowering individuals like you with valuable skills is at the core of what we do.
If you’ve found our free content beneficial in your learning journey, we kindly ask for your support through a donation. Your contribution will not only help sustain the availability of free materials but also enable us to expand our offerings and reach even more learners globally.
Please select a donation method
Full Course on YouTube
Watch the full course in this official PDO YouTube playlist.
Transcript
Welcome to Day #4 of Learn Fusion 360 in 30 days. I’m Kevin Kennedy,
and today we’ll create a complex glass bottle as you learn to use the Loft command. We’ll also look at creating offset construction planes, Intersecting geometry, and more!
Don’t forget to save and name your design file.
The Loft command allows you to connect two or more closed sketch profiles together. We’ll loft between four closed sketch profiles to recreate the example bottle. In addition, we’ll look at adding guide rails to further define the shape.
To get started, let’s create a New Component. Name this ‘Glass Bottle’ before clicking OK. Remember, components will help keep the related sketches and other assets organized, especially as we move on to multi-part models.
To create the first sketch profile we’ll start a new sketch on the XY origin plane.
We’ll use the Center Rectangle command from the origin point. Using the center rectangle instead of a 2-point rectangle will allow us to keep the bottle symmetrical to the center axis. Later in this lesson, you’ll see this makes it easier to mirror our sketch.
We can now type out the desired dimensions as 76mm for the length and 63mm for the width. Remember you can press the Tab key at any time to toggle between the dimension inputs. Once both dimensions are entered, we’ll click with the mouse to place the rectangle.
We’ll use the Sketch Fillet command to add rounded corners for the lower portion of the bottle.
The sketch Fillet can be found under the Modify menu. Once active, select each side of our rectangle. Notice the Fillet command will round over the edges in each corner. We’ll define the fillet radius as 7mm.
It’s important to note that Sketch fillets are not ideal as you’ll see the warning icon letting us know they’ve removed some of the existing sketch constraints. When possible, you’ll want to avoid Sketch Fillets in favor of Modeling Fillets. However, Loft and Sweeps are two common use cases where sketch fillets are unavoidable with many desired shapes.
We can now select “Finish Sketch” as our first profile is complete.
Fusion 360 does not allow you to create regular sketches floating in space. All sketches must be started on an origin plane, a flat planar surface, or a construction plane.
The various types of Construction planes allow us to create a plane by leveraging existing geometry. Offset construction planes are the most common as they simply require an existing sketch or planar face to offset from.
For example, we’ll activate Offset Plane and select the bottom origin plane or the previous sketch. We can then define the specified distance away from the existing sketch. I’ll type out 114mm, followed by the “OK” button.
We can now create a new sketch on this offset plane to sketch out the second profile. Let’s activate the Rectangle tool with the keyboard shortcut letter “R,” as in Romeo. Notice we can then select the construction plane. Activating a sketch command first is another way to create a new sketch.
Before starting to sketch anything we’ll also change the rectangle type to the ‘Center’ option in the Sketch Palette.
Once again we’ll start at the center origin point, and we’ll make this rectangle larger with a length of 95mm and a width of 76mm.
Once the dimensions are in place, set the rectangle.
We’ll add larger sketch fillets this time, using a Fillet radius of 12mm. Be sure to activate the Sketch Fillet tool and not the Solid Modeling fillet command.
Our first two sketch profiles are now complete.
Let’s create two more offset construction planes, allowing us to quickly sketch the circle profiles for the stem of the bottle.
Activate Offset Plane from the Solid modeling tab and select the previous sketch. I’ll define this offset value as 38mm.
Be careful when choosing the object to offset from. If this object changes then the distance of our additional offset plane will change as well. Sometimes you’ll want to offset from the origin plane, as it won’t ever change in location. For this practice project, it’s not a big deal either way.
Let’s create our fourth and final offset plane. This plane will be a distance of 89mm away from the previous plane.
We’ll create two different-sized circles for the stem of the bottle. To quickly activate the circle command I’ll press the keyboard shortcut letter “C,” as in Charlie.
I’ll then click on the lower construction plane. Now that the sketch has been activated and automatically reoriented, start the circle at the center origin point.
Define the diameter as 40mm and place the circle. Take a minute to view the sketch from a side view to double-check you’re sketching on the correct plane. Everything looks correct, so I’ll select “Finish Sketch.”
Once again, I’ll press the keyboard shortcut letter “C” to activate the Center-Circle command. I’ll select the topmost Offset Construction Plane that I just created, and I’ll click on the center origin. This circle will have a diameter of 30mm, as we want the top of the stem to be a little bit smaller.
Once complete, let’s finish the sketch and view the model from the Home position.
We now have our four closed sketch profiles, as each one includes a blue background highlight, indicating they’re fully closed.
On Day #2 of this course, we created the glass soda bottle using the Revolve tool. This more complex bottle shape cannot be completed with Revolve as our shape is not symmetrical in all four directions around the center axis.
We’ll instead activate the Loft command from the Solid modeling tab. Note that Loft is also available in Surface and T-spline modeling, so be sure to activate the blue solid modeling Loft feature.
Once active, we can select our sketch profiles. It’s very important to note that a Loft requires you to select the profiles in the order you want them to be connected. In our case, we’ll start at the bottom profile and select each sequential profile as we work toward the top.
Watch what happens as I select them. You’ll notice it starts to join all of the sketches together, resulting in a 3-dimensional shape.
Looking at the bottle from some different perspectives, you’ll find the shape automatically slopes as it connects each profile. This is not the desired final shape, so we have a few different options to further define the shape.
We can first change the ‘connection’ option to ‘Direction’. This automatically applies an angle based on the sketch plane.
As you can see, this is closer to the ideal shape we’re going for. However, we can still define the Loft with more intention.
We can add guide rails or a centerline to further define the loft shape. Rails are 2D or 3D sketches that influence the loft shape between sections. We can add any number of rails to the loft, but they must touch every profile in the Loft. In our case, the rail will have to touch all four sketch profiles.
Contrary, we can use a centerline down the middle of the shape. However, only one centerline can be used at any given time.
Let’s select “Cancel” in the dialog, so we can sketch our guide rails.
To create the guide rails we’re going to use a combination of the spline tool and the regular line tool. It’s important to note that you can create guide rails with any sketch entities, as long as they touch each sketch profile.
For this project, the spline tool will provide us with extra freedom to tweak the shape of the bottle.
We’re going to sketch this guide rail on the XZ origin plane, as it lies directly in the middle of the bottle.
One thing we’ll want to ensure with the guide rail is that it snaps into each of the four profiles, otherwise, we’ll get a very common error with the Loft command, which states “the guide rail isn’t touching all sketch profiles.”
In order to ensure that our guide rail snaps to each edge of the sketch profiles, we can use the “Intersect” command to reference existing geometry.
You’ll find Intersect in the Create Menu of the Sketch tab, then in the “Project/Include” flyout folder.
Once active, let’s look at the model from the Home position.
As we hover over the sketch lines on the left side, notice the red dot that appears in the middle. This dot represents the area of our existing geometry that intersects the active sketch plane.
By selecting this geometry to intersect, we’re letting the software know that we would like to reference this existing geometry in the current sketch. In other words, it allows us to guarantee that our guide rails are connected to the exact point that touches the sketch profiles.
We’ll select each of the four sketch profiles. Note that the circles will automatically intersect on both sides; however, we only need the left of the rectangles as we’re going to mirror the sketch geometry in a minute.
In the Intersect dialog, make sure the Projection link option is checked. This ensures that our intersected geometry will update automatically if we were to change the dimensions of any of our existing sketch profiles.
Once we select OK, you’ll see that Intersected and Projected geometry is noted with the color purple.
We can now look at the sketch from the Front view.
Let’s start by drawing a regular line that connects the top two circles. Notice the line snaps to our recently Intersected points.
We’ll then activate the Fit Point Spline command. Start from the bottom point and select the next two points. Remember to press the Enter key to commit the Spline, or you can select the green check mark.
Really important, we must take the top spline handle and click and drag it until it snaps to our straight line. This will ensure our guide rail is continuous and treated as one line.
Next, we can select the middle spline point, allowing us to manipulate the spline’s handle. Adjust the handle until you’re happy with the shape of the bottle. Rember, we can also edit the sketch to update this at any time, which is one great benefit of parametric modeling in Fusion 360.
We’re now done with the guide rail on the left. Let’s mirror it over to the right.
Activate the sketch Mirror command. Make sure this is in the Sketch tab and not the Solid Modeling Mirror command.
Once active, we’ll select both the spline and regular line.
If you recall, we started our sketch profiles from the center origin. This means we can simply reference our vertical axis as the mirror line instead of creating additional sketch geometry.
Once complete, select OK.
Notice the mirrored geometry that now appears on the right side.
Reactive the Loft command from the Solid Modeling tab. Select the four sketch profiles in order, as we previously discussed.
We can now select the arrow in the rails section of the dialog, which allows us to define our guide rails. Notice how the shape of the bottle changes as I select each guide rail. Guide rails can help you precisely define Lofts, creating more defined and complex shapes.
If you happened to get a loft error, double-check that your spline and line are connected correctly to each of the four sketch profiles. If those look good, then double-check that the spline is snapped to the straight line, making a continuous line.
At this point, we’ll finish off the bottle by adding a few more details before making the bottle hollow.
If we look at our shape we’ll see that the bottom of the bottle is completely flat. We can activate the Modeling Fillet command and select the bottom edge.
I’ll add a fillet with a radius of 5mm, which adds a nice round-over to the bottom.
Similar to the soda bottle on day #2, we need to apply this fillet before we go to hollow out the body, as the Shell command will follow this contour.
Let’s now create a stem at the top where we can add a thread. I’ll press the keyboard shortcut letter “C,” to activate the center-circle command.
We’ll sketch on the top surface of the bottle. Start at the center origin and define the diameter as 27mm.
We can then activate the Extrude command. Select the circle as the profile to extrude and define the distance as 12mm.
Before selecting “OK,” be sure the operation is set to “Join.” By setting the operation to join, this 3D body will join the existing 3D body, resulting in a single body. This is crucial for the Shell command to work on the entire shape.
We can now activate the Shell command.
Select the top planar surface of the bottle, which will remove the top opening as we define the bottle’s thickness of 2mm.
If the Shell command gives you an error message, you’ll need to edit the guide rails sketch and adjust the curvature of the splines. The Shell command cannot apply the defined thickness if the curvature is too sharp.
Alternatively, try different shell thicknesses to see the maximum size it allows.
Lastly, I’m going to add one more Fillet to the top edge, so this isn’t sharp.
I’ll make this fillet radius 2mm.
You can choose to add a thread to the top of the bottle using Fusion 360’s Thread command.
Activate the Thread command from the ‘Create’ menu.
Start by selecting the cylinder as the face to apply the thread on.
Next, you’ll want to check the “modeled” option, which will make a physical thread in the model. When unchecked, the threads are represented by an image and will not be included in the model if you 3D print or export the file in another 3D format.
The second option in our thread dialog box is the length. It defaults to the ‘Full Length,’ but we can uncheck this to make it shorter by dragging the arrow up or by changing the inputs.
Lastly, you will see that we can define the thread per a number of different thread standards. Take a minute to choose a thread and experiment with adjusting the length.
[Upbeat Music]
Your bottle is now complete! I’ll see you on Day #5 as you learn to 3D model an ice cube tray.
[End Upbeat Music]