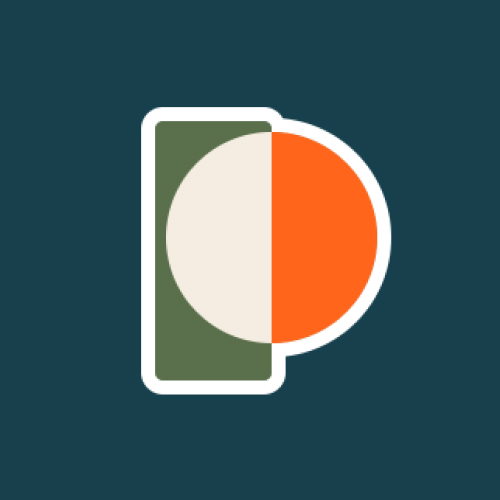
Making CAD education accessible to anyone, anywhere.
We hope you’ve been enjoying the wealth of free Fusion training provided by Product Design Online. Our commitment to empowering individuals like you with valuable skills is at the core of what we do.
If you’ve found our free content beneficial in your learning journey, we kindly ask for your support through a donation. Your contribution will not only help sustain the availability of free materials but also enable us to expand our offerings and reach even more learners globally.
Please select a donation method
Full Course on YouTube
Watch the full course in this official PDO YouTube playlist.
Rectangular Pattern Compute Types
The following three options are available as Computer Types in Autodesk Fusion 360’s Rectangular Pattern Feature.
If Object Type is set to Features, select a Compute Type:
- Optimized: Creates identical copies by patterning feature faces. (Fastest)
- Identical: Creates identical copies by replicating results of original features. Use when Optimized is not possible.
Adjust: Creates potentially different copies by patterning features and calculating extents or terminations of each instance individually. (Slowest)Note: The Optimized setting may cause errors when patterning split features.
Transcript
Welcome to Day #5 of Learn Fusion 360 in 30 days. I’m Kevin Kennedy,
and today we’ll create an ice cube tray as you learn how to cut material out of existing 3D objects, the Rectangular Pattern feature, and more.
I’ve already saved the design file, so let’s get started with a New Component named “Tray.”
We’re going to start by creating a block the size of a standard ice cube tray, followed but cutting out holes for each cube.
Activate the rectangle tool with the keyboard shortcut letter “R”, as in Romeo. We’ll start from the center origin, which will help us fully define this sketch.
We’ll make the length 300 millimeters, the tab key to switch to the other input, and we’ll make the width 104 millimeters.
Let’s then place the rectangle. Notice we can place it in four different directions. This does not matter in the grand scheme of things; however, it will determine which direction our pattern goes later on. Let’s select the upper-right quadrant.
We can now Extrude this sketch to a thickness of 50mm. Remember you can quickly activate Extrude with the shortcut letter “E.”
If we view the model from the Home position, you’ll see that we now have our 3D rectangle, and we’re ready to cut out the ice cube spots.
Let’s create a new sketch on the top surface by right-clicking on the face, followed by “Create Sketch.”
We’ll start with a 2-point rectangle again, not worrying about the location. Let’s make the height 40mm and the width 30mm.
Our rectangle is currently floating in space. If we clear out the rectangle command with the Escape key, we can select and drag the rectangle around.
We’ll use Sketch dimensions to precisely place the rectangle from the edge of the tray.
Activate the Sketch Dimension tool from the Toolbar. Sketch Dimensions require you to select two sketch curves, followed by defining the distance or angle between them.
We’ll select the top of the rectangle, followed by the top of the 3D body. Once you select two sketch curves, you’ll see that we can place the sketch dimensions. Where you drag the mouse cursor will determine how the dimension is applied.
We’ll then click to place the dimension to the left of the 3D body. Let’s define this dimension as 7mm, which will make the rectangle 7mm from the edge.
Another way to apply a dimension is to select the lines or geometry first. Hold the Shift key and select both vertical lines on the left. We can then activate the Sketch Dimension tool, making this 7mm as well.
We’re now ready to cut the shape out of the existing 3D body. This can be achieved using the Extrude command from the “Solid” tab.
Once active, select the rectangle if it’s not already.
Let’s view the model from the Home Position, making it easier to see the cutout.
The Extrude command lets us cut away from existing 3D bodies by dragging the blue arrow into any existing 3D body. Notice the red preview that indicates which area will be cut away.
You’ll also see the “Operation” changed to “Cut” in the Extrude dialog. You can manually change this at any time if it doesn’t automatically.
Let’s define the distance as 30mm. It’s important to note that you must include a minus symbol to make this cut into the existing 3D body.
In the Extrude dialog box, you will also see that we can add a taper to the Extrude. The taper will help ensure that our ice cube can fall from the tray. Let’s define the taper angle as -10 degrees.
Notice how the cube is now angled on all four sides. Let’s click OK to confirm the Extrude cut.
Let’s add a Fillet to the edges before we create the remaining cutouts.
With Fillet active, we can select all of the inner faces while holding down the Shift key. Use the ViewCube to reorient the model as needed.
Once all the faces are selected, we’ll define the Fillet radius as 4mm.
Now that our first cutout is complete, we can activate the Rectangular Pattern tool. As with many features, the Pattern features are available in both the sketch environment and the Solid modeling environments. Be sure to activate the solid modeling Rectangular Pattern command.
Once active, we’ll change the “Object Type” to the “Features” option. This allows us to select the Extrude and Fillet commands in our parametric timeline, resulting in them being patterned.
We can now choose the direction of the pattern. We’re going to pattern in both directions so we’ll select both the length and the width of the 3D body.
Notice our dialog box now has many additional options. Before we edit those, I recommend selecting and dragging each of the blue arrows in the desired direction. This will help us see what’s going on.
We can also look at this from the Top View.
For the Length, we’ll make the quantity 7. This will make 7 cubes for the long side.
The Distribution is then calculated in one of two ways. Either by the Full Extent or “length” of the pattern or by defining the “spacing” between each pattern.
I’ll use the “Extent” type as I know the distance is 255mm.
For the other direction, we’ll set the Quantity to 2. We can then set the distance to 50mm.
Before selecting “OK,” take note of the “Compute Type.” This will determine how the pattern is computed and may affect the performance of the software. Let’s change this to “Optimized” which takes the least amount of processing power from your computer.
I’ve also placed explanations of each Compute Type below this video.
Now that our cutouts are complete, we can finish off the bottom of the tray. On days #1 and #4 we used the Shell command to hollow out objects. Today, we’ll take a look at how the Shell command works when you select more than one face.
Activate Shell from the Toolbar.
Once active, select the four side faces of the 3D body, as well as the bottom face.
We can then define the Shell thickness as 2mm.
The Shell command will trace the existing cutout shapes to create the desired thickness throughout.
To complete our tray, we’ll add an edge that runs around the perimeter.
Let’s start by adding Fillets to each of the four corners. Be sure to activate the Solid Modeling Fillet and apply a radius of 10mm.
To create the edge, we’ll sketch a side profile, which will allow us to Sweep it around the entire edge of the tray.
We want the sketch to be in the middle of the tray, which will ensure it’s connected to the existing edge. To sketch in the middle, we’ll need to add a Midplane construction plane.
Activate Midplane from the dropdown menu, then select the outer face on each long side of the tray.
Notice this places the construction plane directly in the middle of the two selected faces.
Let’s create a new sketch on the midplane.
Zoom in so it’s easier to sketch.
We’ll use the regular Line command to create a backward “L” shape, without worrying about the dimensions. However, make sure the automatic sketch constraints keep your lines vertical and horizontal, as applicable.
Let’s add some Sketch dimensions. Starting with the top line, we’ll make this 2mm. The left vertical line will be 3mm.
The bottom line will be 5mm. Instead of applying another 2mm dimension to the line on the left, we will use Equal constraints. Always use constraints over dimensions, when possible. This will keep your sketches simpler and easier to maintain in a parametric manner. Constraints are a critical concept that we’ll continue to discuss throughout this course.
Activate Equal and select the two lines.
You’ll also see that our sketch can move around freely. We’ll use the “Coincident” constraint to force the corner to stay on the edge.
We can now activate the Sweep command from the Solid Menu.
Select the recent closed-sketch profile.
For the Sweep path, you’ll find that we don’t always need to create a new sketch. We can instead select the existing edge of the tray.
Double-check that the profile sweeps all the way around the model, and that the operation is set to “Join” the existing 3D body.
Last but not least, apply a 1mm fillet to the four edge lines around the outer contour, making sure the edges are not sharp.
[Upbeat Music]
You’ve successfully completed the Ice Cube Tray!
I’ll see you on Day #6, where we’ll 3D model a Hex Nut.
[End Upbeat Music]