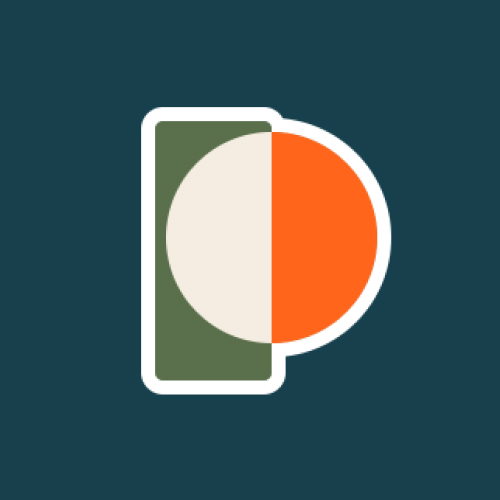
Making CAD education accessible to anyone, anywhere.
We hope you’ve been enjoying the wealth of free Fusion training provided by Product Design Online. Our commitment to empowering individuals like you with valuable skills is at the core of what we do.
If you’ve found our free content beneficial in your learning journey, we kindly ask for your support through a donation. Your contribution will not only help sustain the availability of free materials but also enable us to expand our offerings and reach even more learners globally.
Please select a donation method
Full Course on YouTube
Watch the full course in this official PDO YouTube playlist.
Transcript
Welcome to Day #7 of Learn Fusion 360 in 30 Days. I’m Kevin Kennedy,
and today we’ll create a Bike Handlebar Grip as you learn to create Text, use the Emboss Tool, and more.
Let’s get started with a New Component named “Grip.”
We’re going to start by sketching the side profile of the handlebar using the Center Circle command. Create a new sketch on the XZ origin plane and start the center circle at the origin point.
We’ll make the diameter 30 millimeters.
Let’s now use the Extrude command to make our cylinder with a length of 125mm.
Our basic cylinder provides a 3D body that we can now Emboss or Deboss text on. We’ll then finish off the model with a pattern and some additional details.
We’ll want to create our text near the existing 3D body in preparation for the Emboss tool. Let’s create a new sketch on the YZ origin plane.
Once in the Sketch Environment, we can activate the Text command from the Create menu.
I also prefer to use the Shortcuts box. Press the keyboard shortcut letter “S” and simply type the feature you’re looking for. You can press Return to activate it or click it with your mouse.
Once active, the Text command requires you to define the bounding box. This is similar to graphics programs. Let’s click anywhere in the upper left corner, followed by the lower right corner.
We’ll eventually dimension the bounding box to the edge.
In the Text dialog, type your name or the desired brand name.
You can then take a minute to choose your desired font, followed by defining the text height and character spacing. All of these are personal preferences.
Lastly, you’ll see that we can left-align, right-align, or center-align the text in both directions. I’ll go ahead and center align it, making sure the text is always in the middle, once we finalize the bounding box.
Click OK once you’re satisfied with your text.
If I click and drag on the corners or edges of the bounding box, you’ll see that it moves around freely. Just like regular sketches, you’ll want to fully constrain your bounding box to ensure your text maintains the desired location.
We’ll need to use the Intersect command, activated from the Shortcuts Box, to reference the corner points of our existing cylinder. Select the edge and notice how all four corner points are projected into our existing sketch.
With the Coincident constraint active, we’ll select the corner of the bounding box and the corner of the model. Do this for both corners.
Our sketch is not yet fully defined. We’ll need to add either a vertical or horizontal constraint to one of the lines.
Double-check that your sketch is fully defined by finding the red lock icon in the Browser.
While you’re here, take a minute to rename your sketch.
We’re now ready to activate the Emboss tool from the Create Menu of the Solid tab.
The Emboss tool raises or recesses a sketch profile relative to the faces of our solid body. We’ll start by selecting the desired sketch profiles. In our case, we’ll select the text.
Next, we need to define the 3D body we’d like to emboss, so I’ll select the face of the cylinder.
To make this easier to see, I’ll turn off the Sketch and zoom in.
Notice the text is now Embossed and we have additional options in the Emboss dialog.
We can change the depth to 1mm, or the desired thickness.
We can also toggle the Emboss to a Deboss, which removes material from the selected faces on the body.
Use the Flip icon to fix the Emboss if yours is facing the wrong way.
You’ll see that we can also adjust the alignment by dragging the arrows and slider or by defining values in the dialog.
This looks great so far, so I’ll click OK.
We’re now going to right-click on the leftmost face and we’ll create a new sketch.
Sketching on this side profile will allow us to create the first “ring” of the grip pattern.
Let’s first press the shortcut letter “P,” as in Papa, to activate the Project command. We’ll project the edge of the cylinder to ensure our grip texture always adapts to any changes in size. Taking these steps is critical in creating parametric models.
We can then use the Offset sketch tool to create an additional circle 1.5mm away from the existing edge.
With Offset active, select the edge and define the Offset distance.
Before we Extrude the shape, let’s draw two lines to block the section around the letters.
Activate the Line tool and draw two lines connecting the circles. We can always adjust the position later.
Let’s Extrude this profile shape to a distance of 1.5mm. Make sure it’s heading toward the letters. If not, you may need to add a minus symbol to flip the direction of the Extrude.
Lastly, make sure to set the “Operation” to “New Body.” This will leave us with a separate body in the Browser, making it easier for us to pattern.
Notice in the Fusion 360 Browser how we can turn this specific body on and off as needed.
With the Rectangular Pattern tool, we can set the “Object Type” to Bodies and select this individual body to pattern. This would not be possible had we joined the body to our existing cylinder body.
I’ll click the Axes selector, followed by the Y-Axis. Drag the blue arrow over to get the pattern started. You can then play around with the various quantity and spacing options.
I’ll set mine to the Spacing Distribution, with a quantity of 50 and a distance of 2.5mm.
Looking at the pattern, I’d like the two rows on each end to be fully closed. Unfortunately, we cannot Extrude this or use the Offset face command as they’ll affect each body in the pattern.
Instead, we’ll use the Sweep command in a similar manner as Day #3, the paperclip lesson.
With Sweep active, we can select the four inner faces of the grip. You’ll then want to use the Path selector to reference the existing edge of our Cylinder. Notice the Sweep command can leverage existing geometry and you don’t need to create sketch profiles, or a path, each time.
Make sure to set the operation to “New Body” before clicking OK.
We’ll use the Shell command to hollow out the cylinder.
Select the left face and set the thickness to 2 millimeters.
You may end up getting an error message because our Embossed Text is part of the 3D body and the Shell command cannot effectively trace the inside of some letters.
This is not a problem, as one great benefit to Fusion 360 being parametric is that we can change things that we may not have planned for.
We can clear out the active command with the Escape key and roll the timeline marker to just before the Emboss command.
Complete the Shell with a thickness of 2mm, then drag the timeline marker back to the end.
You may have noticed we have a ton of 3D bodies in the Fusion 360 Browser. It was originally important that we kept the grip as a separate body for us to complete the pattern. However, if we no longer have a reason for them to be separate we can simplify our file by using the Combine command. With Combine active, we select our target or “Main” body, which is our cylinder. We can then select an unlimited number of bodies to join the target body.
You can easily select everything by holding the Shift key and pressing the last body in the list.
Notice you can also use this approach to cut or intersect existing bodies with the target body.
After you select OK, you’ll end up with a single body in the Fusion 360 Browser.
We can finish off the model by creating a larger cylinder on the left side.
Create a new sketch and start by projecting the innermost edge.
Once the inner edge is projected, we’ll create a final circle by offsetting 8 millimeters from the outer edge.
Extrude this to a depth of 1.5 millimeters, making sure it’s going away from the Text. You can also set this operation to “Join” if it’s not already.
One last tip for today’s lesson, if you’d like to play around with adding appearances. Activate the appearance command with the shortcut letter “A.”
Search for “Rubber” and make sure to download the material if you have not already. Drag and drop it onto the model. This will automatically apply the appearance to the entire model as we have only a single body. However, you can select individual faces to apply a unique color or material. For example, I’ll hold the shift key and select each individual face of the letters.
Once selected, I’ll drag and drop a blue appearance onto the face, carefully releasing the cursor within the highlighted area of the selected faces.
Notice this applies the appearance to only the faces of each letter, without affecting the rest of the 3D body.
This is a handy trick to know when adding colors or appearances to your models.
[Upbeat Music]
You’ve successfully completed the bike handlebar grip. I’ll see you on Day 8, where we’ll model a standard doorstop.
[End Upbeat Music]