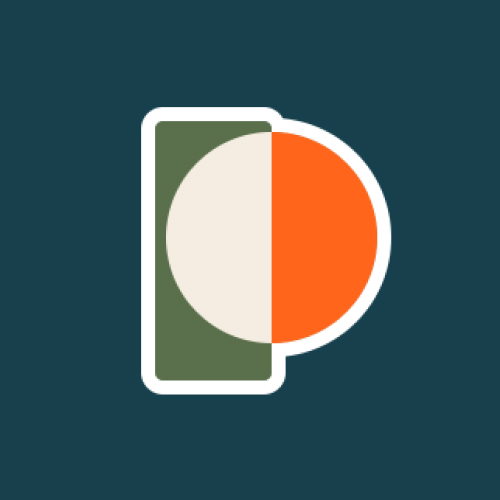
Making CAD education accessible to anyone, anywhere.
We hope you’ve been enjoying the wealth of free Fusion training provided by Product Design Online. Our commitment to empowering individuals like you with valuable skills is at the core of what we do.
If you’ve found our free content beneficial in your learning journey, we kindly ask for your support through a donation. Your contribution will not only help sustain the availability of free materials but also enable us to expand our offerings and reach even more learners globally.
Please select a donation method
Emboss Update (October 2023)
At approximately 10:11 in the video – The new emboss tool works on more surfaces, but has also impacted how the Emboss tool worked when this tutorial was recorded.
Solution:
- Activate Emboss
- Uncheck ‘Tangnet Chain’ in the Emboss dialog. *** Very important. This must be done ***
- Select the four sketch profiles (two halves of the circle, two rectangles)
- Switch to the ‘Faces’ selector in the Emboss Dialog
- Select the top face of the doorstop (the largest face).
- Hold the CMD Key (Mac) or CTRL Key (Windows) to select the two remaining top faces.
- Select OK to confirm the Emboss.
Full Course on YouTube
Watch the full course in this official PDO YouTube playlist.
Transcript
Welcome to Day #8 of Learn Fusion 360 in 30 Days. I’m Kevin Kennedy,
and today we’ll create a Rubber Doorstop as you learn to use the Chamfer tool, more complex fillets, offset faces, and more.
I’ve already created a Component named “Doorstop.” Remember that components will keep our sketches and 3D bodies grouped. They’ll also be critical in applying Joints in multi-part models, so I encourage you to use them every time you get started, even when the file may start as a single-part file.
Let’s start a new sketch on the YZ Origin plane, as we’re going to start with the side view of the doorstop.
With the Line tool, start at the center origin point. I’ll sketch out the side triangle shape, with the addition of a vertical line on the front. Don’t worry about the dimensions at this point, just complete the rough shape.
The vertical line will leave us with enough thickness to eventually add a Chamfer.
Now that we have our rough shape, we’ll want to think about how we may add constraints before adding sketch dimensions. Notice an automatic perpendicular constraint and vertical constraint were applied.
Currently, the top line and leftmost line can be moved around. We’ll add sketch dimensions to fully define our sketch.
Let’s start by selecting the bottom line and we’ll make the overall length 100mm.
We can also add sketch dimensions between sketch points and lines. For example, let’s select the topmost point and the bottom line. Place the sketch dimension to the left, and we’ll define this as 30mm.
Fusion 360’s Sketch dimensions allow equations as well as the ability to reference each other. If we want the front line to remain a third of the overall height, we could place the dimension. Select the existing height dimension and notice it references the dimension number “d2” as this is the second dimension we’ve placed. We’ll do a forward slash to divide, and the number 3. After pressing the Return key, you’ll see our dimension is calculated. This dimension will automatically update if we change the original height dimension.
Lastly, we’ll select between the top and bottom lines, allowing us to define the angle between them. This will be the desired angle of the doorstop. I’ll define this as 12 degrees.
Notice how this final dimension makes all of the sketches the color black, and we should now have the fully defined “red lock icon” in the Browser.
We can now turn this into a 3D body by Extruding this to a width of 35mm.
Our basic shape of the doorstop is now complete. We’ll finish off the model by adding the appropriate Fillets and Chamfers, followed by an additional skirt at the bottom.
We’ve used the Fillet command several times throughout the first 7 days. While Fillet helps us make a nice round over, the Chamfer tool helps us create a bevel or ‘sloped’ edge.
Activate Chamfer from the Modify dropdown and select the upper edge. Watch what happens if I drag the arrow down. You’ll see this applies to the Chamfer based on the default of ‘Equal Distance.’
Many times, we’ll want to control the chamfer angle by either defining the angle itself or by defining the distance in both directions. Both of these options are available in the Chamfer dialog.
I’ll make the distance 15mm and the angle 25 degrees.
Let’s also apply Fillets. Typically fillets will always come after Chamfered edges. With the Fillet command active, I’ll select the top two faces, as well as the back two corner edges and the front two corner edges.
Define the fillet radius as 3mm.
Note that selecting faces will automatically apply the fillet to the four edges of the face. This saves us time from having to select each edge individually.
I’d also like this bend here to be more rounded over. We can fix this by adding an additional fillet size in the Fillet dialog. I’ll define this fillet as 20mm.
We can also view this from the side view and manually adjust this by the blue arrow. Something like 45mm may provide us with a more desired roundover to help this get underneath the door.
Let’s now create a ‘skirt’ or additional surface material on the bottom to help prevent the doorstop from sliding.
Flip the model around and create a new sketch on the bottom.
We’ll start by using the Project command to project all of the existing edges into our current sketch. This allows us to reference them.
I also like to adjust the ViewCube arrows so I’m looking at this with the model in a vertical orientation. This will help us think about symmetry.
Let’s sketch a line running down the middle that we’ll later use as a Mirror line.
We can then start a new line at the lower left point where the fillet radius starts. This line will run to the back of the doorstop as it flares out.
I’ll then make a final line that runs 10mm to the left, starting at the top corner edge.
Make sure to apply a Horizontal constraint if one is not automatically applied.
We’ll then use a Coincident constraint to force our previous line to connect to the end of this line.
To create the other side and our arc curvature, we’ll want to turn this middle line into a center line. This will allow us to reference it with the mirror command and ensures it doesn’t affect other geometry. Select the line, followed by the “Centerline” option in the Sketch Palette.
We can now use the Sketch Mirror command to mirror the two lines over to the other side. Select each line and notice that because we designated the centerline as a centerline, Fusion 360 automatically selects that as the mirror line.
One important thing to remember is that Mirror is also available in the Solid modeling environment. Generally, it’s considered a best practice to only mirror small and simple sketches. For more complex geometry, complete the mirror in the solid modeling environment. In scenarios like this, the advantage is that we can now complete our sketch with the desired arc.
I’ll use the Tangent Arc command which automatically applies tangency to the adjacent geometry. This ensures you end up with smooth geometry.
Keep an eye out for each tangent constraint. If you don’t see one on each side, you’ll want to manually add the Tangent constraint.
Let’s now Extrude this to 2mm. Make sure to add the minus symbol so that it’s heading toward the existing 3D body.
You may have noticed we have some strange geometry where this Extrude meets the fillet.
Let’s edit our sketch by double-clicking on the sketch in the parametric timeline.
I’ll delete the coincident constraint that is holding this line to the projected line. Let’s snap it back to the projected line, followed by dimensioning 10mm between the two.
I also didn’t like how large the Tangent arc was, so I’ll select that and press the Delete key.
Instead, I’ll use the 3-point arc command. This allows us to select the starting point and the endpoint of the arc, followed by a point on the arc
I’ll use the Sketch dimension tool to define the radius of the arc, such as 35mm. Feel free to experiment with this and find a radius that you prefer.
When you select “Finish Sketch” you’ll see that our Extrude is automatically updated. Once again, we’re seeing how efficient parametric modeling can be.
We’re now ready to hollow out this design using the Shell command. Remember that Shell will effectively trace the contour of the selected body. With that in mind, we want to revisit our previous Extrude and make sure our 3D body is separate from the main body. This should be set to “New Body” instead of “Join”.
We can now use the Shell command on the bottom surface of the main body, making this have a thickness of 2mm.
The shell looks great, but you may have noticed we ended up with a gap between our main body and the skirt. Let’s go ahead and remove this gap by selecting one of these inner faces. We’ll activate the Offset face command, as not to be confused with the Offset sketch command. Bring this in half a millimeter which will fill the gap.
I’d also like to add Fillets to the sharp edges of the skirt body. Let’s add a 1mm fillet to the top three edges. I’ll define a second radius of 5mm for the two vertical edges, helping ease this transition.
We’ll finalize our doorstop design by adding friction strips across the top.
This can be done in a number of ways, including Sweeping a profile, Lofting a complex shape, or utilizing the Emboss tool.
Using Emboss will allow us to create a simple sketch without worrying about this complex curvature. Emboss will automatically wrap the shape around the top surface.
Let’s create a new sketch on the top surface. We’ll start with a standard 2-point rectangle that has a width of 2mm and a length of 90mm.
I’ll use the sketch dimension tool to dimension this 2mm from the top and left edges.
Looking at the sketch, you’ll see that this rectangle is not sticking past the edge of the doorstop. This is very critical as the Emboss tool cannot wrap shapes that are longer than the target object.
Before we Emboss this, let’s add a circle to the end. We can do this with a Center Circle or the 2 Point Circle. 2-point will allow us to simply select the two corners of the rectangle.
Activate the Emboss tool and select the four profile sketches.
Switch to the Faces selector, followed by selecting the top face of the doorstop.
I’ll set the ‘Depth’ to 1mm, followed by OK so we can take a look at the results. Notice how Emboss nicely wrapped our simple rectangle around this curvature.
We’ll finish the rest using the solid modeling Rectangular Pattern feature.
Change the ‘Object Type’ to Features and select the Emboss feature in the timeline. This will repeat our embossing throughout the pattern.
We can select any horizontal line for the Axis, and drag the blue arrow over to get our pattern started. Then, take a minute or two to create a pattern that you like.
I’ll make mine a quantity of 6, with an Extent distance of 23mm.
Last but not least, let’s add a 1mm Fillet to all of the top ridges, making sure they’re rounded over.
You may also find it fun to play around with adding a rubber or plastic appearance.
[Upbeat Music]
You’ve successfully completed the doorstop! I’ll see you on Day 9 where we’ll model a lightbulb.
[End Upbeat Music]
Leave a Reply