Orange Peeler Example
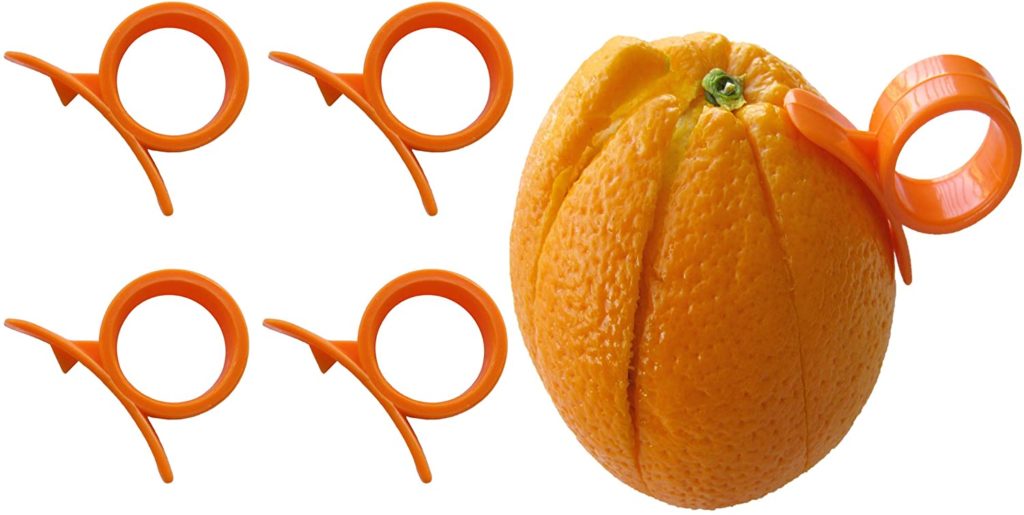
This is one of the orange peelers that I referenced on Amazon – https://amzn.to/2A4afir
There are several others on Amazon, as well as other sites. I used a combination of dimensions and guesstimates based on several reference photos and product descriptions.
Books on Human Factors
Understanding Human Factors is beneficial if you’re serious about a career in design and engineering. These are two of my favorite books that discuss Human Factors and Anthropology concepts in relation to design.
Calipers
I’ll be demoing some reverse engineering with the use of Calipers in a future video. I’ve been asked by several people which caliper I recommend – which is a tricky question! Calipers range from $20 to hundreds of dollars.
There are several “cheap” calipers that are sufficient for reverse engineering parts for 3D printing. Here are some tips to use when looking for a good yet affordable caliper.
- Avoid ones with plastic bodies
- Avoid digital calipers on the low end (the digital aspect often breaks or causes issues)
- Look for one with several (hundreds) 4+ star reviews
- Look for one that comes with a hardshell case
($15-60) Vernier Caliper – Beginner/Budget Choice
This is my favorite one to recommend to beginners or those looking to just use it once a month. A vernier caliper includes the dimensions as lined increments, which means you won’t have a dial or digital screen that craps out after the first use.
($100+) Dial Caliper – Intermediate Choice
Dial-based calipers are a great option for those not looking to spend $200+ on a fancy digital one. This one is created by the famed Mitutoyo, but be aware that these “intermediate” level calipers are not made in Japan like the high-end ones.
($200+) Digital Caliper – Serious Investment
If you plan on doing a lot of reverse engineering or have the need to use a caliper on a daily/weekly basis, then I highly recommend you invest in a top of the line digital Mitutoyo. Make sure to double-check you’re ordering one Made in Japan, otherwise you’re getting a knock-off.
Transcript
Let’s take a look at how to reverse engineer this 3D printable Orange Peeler.
Hey there, it’s Kevin Kennedy, and welcome to episode number 8 of Practical Prints. A YouTube series where I show you how to design 3D printable objects in Fusion 360.
Someone asked me a few questions about reverse engineering one of these nifty little orange peelers, and my first thought was that this could be an interesting tutorial.
The object seems pretty simple…but one of the challenges is that I don’t have the actual product to reference. If I had the object in hand then I’d grab a pair of calipers and we could easily measure everything. Instead, I wanted to take you through some of the steps that I often take to reverse engineer something while only using reference images and other details found online.
This is the original image that was sent over with the questions. First, before doing any work, I like to always figure out how the object was originally manufactured. That can help us determine some critical details.
Looking at this photo, you’ll notice there is a parting line running straight down the middle. This tells me it’s very likely that the object was injection molded with a 2 part mold, which is very feasible since the object is symmetrical.
Knowing how it was manufactured will also help us consider the thickness, among other things, as we start to recreate this in Fusion 360.
Before jumping into Fusion the next thing I like to do is figure out a good starting point for the model. I often look for a simple shape, as well as a part of the model that can act as the base for creating other parts of the design.
With this design, the circle seems like a great place to start as it’s an easy shape to define, and then we can build the attached arc and the cutting portion.
Jumping into Fusion 360, let’s create a new sketch on the top origin plane.
We can then activate the center circle and start from the center origin point.
If you do a quick Google image search for Orange Peeler, you’ll find that this design is set up so the user’s thumb fits within this circle.
Using that knowledge, we can define the inner diameter of the circle. The great thing about designing for 3D printing is that you can measure the width of your thumb to ensure this design works for you. Otherwise, if we were designing the original product for the masses, then we would want to rely on Human Factors studies. I’ve added some links to my favorite Human Factors books to this tutorials resource page.
You can also do a quick Google search, where you’ll find that several studies say the average thumb width is 25mm. Let’s enter 25mm for the diameter of the circle.
We now want to create the thickness of the thumb hold, which we’ll do with the offset feature. I’m going to add an offset of 2mm, which will be the thickness of the print.
We can now extrude this to a width of 14mm. This dimension is just a guesstimate based on the images.
Another great tip if you’re reverse-engineering something solely from photos is to find the product for sale and look at the product description. You’ll often find the product dimensions. If you’re lucky, you’ll even find a listing that includes a 2D dimension drawing or user reviews that include photos with a tape measure.
The next portion we need to create is the arc.
Let’s create a new sketch on the top face of this cylinder.
We can then create a 3-point arc out in space.
Looking at the product description, I found that the overall length of one of these orange peelers is 60mm.
We can use the Sketch dimension tool to define the width from the starting point to the endpoint of the arc.
We’ll also want to make sure the endpoints are straight across, so we can add a horizontal constraint to each endpoint.
At this point, we want to position the arc so it aligns with the circle. One thing that I discovered while browsing online is that there are several different variations of this product. Some of them have the circle off-center, while others are centered and symmetrical.
For simplicity, let’s keep ours centered. We can do this by adding a vertical constraint to the arc’s center point and the origin point, which forces the arc to stay directly in the middle.
We also want to define the radius of the arc. This is something that you’ll find a bit more challenging to find a dimension on without the actual product. However, if you wanted to be specific you could think about the use case. Remember, this portion is supposed to wrap around the shape of the orange. You can try to find the average diameter of an orange… or we can print some out and adjust accordingly.
I’ll make the radius of mine 40mm, which I got from tracing and measuring one of the reference images.
Lastly, we want to position the arc so that it overlaps with our existing 3D body.
Let’s project the geometry of both circles. With the project command, we simply need to select each circle, and their geometry is projected to our current sketch, allowing us to reference them.
I’m also going to create a line that runs from one circle to the other. First, we’ll want to use vertical constraints to make sure the line is truly in the center.
We’ll then use the midpoint of this line to create a place for the arc to snap to. However, let’s first turn this into a construction line.
The arc has no place to snap to, so we’ll need to activate the point feature, followed by placing a point where it snaps to the midpoint or center of the arc.
We’ll also place a sketch point on the center of our construction line.
We can now shift-click both sketch points and add a coincident constraint, which will force the arc to snap to the correct position, resulting in a fully-constrained sketch.
We can also offset this arc 2mm to create the thickness of this portion.
Notice we may have to flip the offset to get it on the correct side.
We need this arc shape to be closed off so we can Extrude the closed profile. To close off the shape we can simply connect them together by adding lines on each end.
With the extrude command we can add our same thickness of 14mm. However, I’ll use the “To Object” Extent type, which lets us choose the bottom face, ensuring it’s always the same thickness.
We also want to make sure the Operation is set to “Join” so this 3D body joins the existing 3D body.
At this point, we have the basic shape down.
One thing you may notice looking at the reference images online is that most of them have support in between the circle and the arc. The support appears to be only a few millimeters thick in the center of the object. Keeping in mind that this is for 3D printing we can make ours the entire thickness of the design so we don’t need to print supports for this portion.
To create this, we’ll create another new sketch on the top face.
To get the geometry to be continuous we can create a tangent arc between the circle and the arc. However, we cannot use the tangent arc command because it only works if you start from an endpoint.
Instead, let’s create a 3-point arc by snapping each endpoint to existing geometry. One will snap to the arc and the other will snap to the circle. We can then place the third point.
We can now select the tangent constraint in the toolbar, followed by clicking on the arc and one of the connected objects… and we’ll have to do the same for the other side. Notice how that creates tangency, making this shape smooth and continuous.
I’ll add a sketch dimension of 4mm, to make sure this sketch is fully-constrained and so the arc cannot be moved.
Let’s also create a construction line down the middle, so we can mirror this object over to the other side.
With the sketch mirror command, we can mirror the arc over and we can extrude these profiles down… once again using the “To Object” Extent Type.
We’re now ready to create the cutting portion that cuts through the skin of the orange.
So far, we’ve made a lot of guesstimates based on reference images and product descriptions. You’ll find that a lot of times that is sufficient when trying to reverse engineer something without the actual product.
However, using calipers and a product in hand can produce better results, especially with more complex objects. If you’d like some tutorials on reverse-engineering objects with calipers then let me know by commenting your ideas of what objects would be interesting to reverse-engineer.
We want the cutting portion to be created in the middle of our existing 3D body, so let’s use the midplane construction option. That will let us select both the top and bottom faces of the model.
We can then right-click to create a new sketch on this midplane.
Looking at the original reference image, you’ll see that the cutting tool is a V-shape, and it appears to be offset to one side of the arc.
Let’s first create two lines that connect to the arc, resulting in the V-shape. We’ll then dimension and constrain it.
One quick thing to point out – I have the Auto Project Edges on Reference setting turned on, which is why I’m able to snap to these existing 3D bodies. If yours isn’t snapping then you’ll need to turn this setting on in your Preferences.
With our triangle sketch, we can add a sketch dimension to one line. The size of our triangle is a bit hard to decipher solely from reference images. However, looking at the thickness of the plastic we can guesstimate it’s about 4-6mm in size. I’ll use 5mm for the length.
We can also add an equal constraint to both lines, which makes sure they’re both 5mm.
Several of the images online also look like the cutting tool is vertical, so we can add a vertical constraint to the line on the left.
Lastly, we want to dimension this triangle in place. It appears that the triangle is positioned near the edge of our circle. Adding a sketch dimension from the triangle to the end of our arc, we can define a dimension until it’s positioned in the approximate location.
It looks like a dimension of 14mm will take care of this.
We can then hit the keyboard shortcut letter “E,” as in Echo, for the Extrude command. Our closed profile should be automatically selected because we only have one profile.
Remember we created this sketch in the middle, so we’ll want this extrude to run in both directions. Let’s change the Direction type to Symmetric. We can then define the distance as 1mm, making sure the Measurement option is set to half-length.
The cutting tool is now complete. However, in its current state, it would require the use of supports. One consideration would be to add a taper to the sides of this triangle, so this can be printed without supports. That may also affect the way this cuts, so I decided to simply print out my initial test prints with supports.
Looking at the reference image, we’ll see that the last details we need is this chamfer that runs up to the cutting tool. Note that it also follows this rounded curvature of the front.
We’ll first want to add a fillet of 7mm to the front two edges. I’m using 7mm because it’s half of our model’s width. We can use the “Add New Selection” option to include the back two edges. I don’t want the back corners to be sharp, but I always want them to be different from the front…so I’ll add a fillet of 3mm.
I would advise against making the fillets the same, as this small detail will help us easily determine which side the cutting tool is on. Especially while it’s pressed into the orange skin, we’ll know the direction we should be cutting.
To create this chamfer we’ll need to split our body at the point we want our chamfer to end, that way we can reference only that portion of the sketch. Otherwise, if we select these edges, the chamfer will be applied all the way around the model.
It appears the chamfer runs up to the cutting tool, so I’m going to create a construction plane at the front of it. Let’s use the option “Plane through Two Edges,” which will let us select both edges of the triangle. We can then use the split body command, using the construction plane as the splitting tool.
With the Chamfer tool active, we can now define only the front portion of this edge.
Let’s also change the chamfer type to “Two Distances,” which will let us better define the distance in each direction.
We want this direction to be a minimum of 1mm, so our model has enough thickness.
In the other direction, we can drag the arrow until it appears similar to our reference image. It looks like we need about 4mm.
Overall, it looks like we were able to recreate this design with some basic research and some guesstimates based on the reference images. Again, this isn’t as ideal as having the object in hand with a set of calipers… but you can often make things work by analyzing proportions and referencing human factors or product descriptions.
To summarize, I would recommend checking out product descriptions and reviews if you’re looking to reverse engineer basic parts without being able to measure the actual object. The great thing about Parametric Design is that you can continue to tweak the object’s dimensions as needed, keeping in mind that the manufacturing method is different and things can be tweaked based on printed results.
Last but not least, I want to give a quick shoutout to those who supported my content over the last two weeks.
Thanks to the new Patrons…
Jason, Henry, Nathan, Frits, Bruno, It’s a Munk, Tom, Dmitriy, Caroline, Phillip, Peter, Keith, Meryl, Tomm, John, Bryce, T1Toine, and the anonymous contributor.
And thanks again to those who supported the channel via my Buy Me a Coffee page…
Tony, Leonardo, Roger, Fastline Racing, Van Linh, Iflam3s, Millie’s Pizza, Kami, Robert, @Steve, Adam, Ronald, Digital Document Systems, and of course the anonymous contributors.
Be sure to hit the subscribe button so you don’t miss out on new tutorials that are released every Friday. Then, click that playlist in the lower right-hand corner to watch the rest of the videos from this series.
Leave a Reply