Learn how to create multi-color prints with 3D printable inlays designed in Fusion 360. I’ll show you how to cut text out of another part after adding chamfered edges to it.
We’ll also look at using the boundary fill command to create a positive shape out of a negative void. Be sure to stick around until the very end where I’ll demo the final 3D prints.
Products I Used
Here are the products that I used to complete this 3D Printed keychain with a different color of inlay.
- Hatchbox Wood Filament – https://amzn.to/2TRxdBi
- Orange PLA – https://amzn.to/36r2RrP
- JB Weld Epoxy – https://amzn.to/36q9Jpw
- 1000 Grit Sandpaper – https://amzn.to/2RpDItE
- Key Rings (pack of 12) – https://amzn.to/38xYcG0
- Irwin Quickgrip Clamp (4 Pack) – https://amzn.to/37tUGMM
Gluing the Inlay
- To glue the inlay I used JB Weld Epoxy.
- Be sure to clean out any strands or print imperfections before you put glue in the letter cavities.
- Lay the glue in the cavity of the inlay, as it’ll be hard to handle the inlay with glue on it
- I then placed the letters in each cavity, one at a time.
- After the letters were glued and in place on each side I wrapped it in parchment paper (to keep the clamps from getting glue on them) and clamped it with an Irwin Quickgrip clamp, which was the perfect size for the keychain!
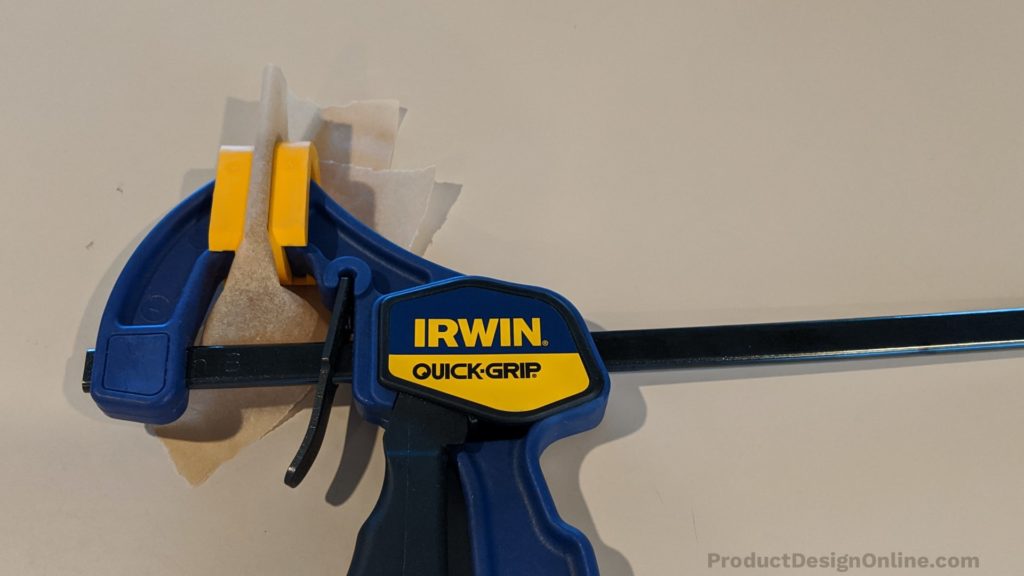
Transcript
Hey there, it’s Kevin Kennedy and welcome to episode number 3 of Practical Prints.
By the end of this video, you’ll know how to create 3D printable inlays for multi-colored 3D prints. Within Fusion 360, we’ll look at using the combine tool to cut away components, we’ll add drafts or chamfers to the inlays, and we’ll factor in clearance for the mating parts.
Before we start modeling, I should state that this approach is intended for those who don’t have a 3D printer with a dual extruder…and for those projects where filament changes won’t work. We’re also going to add the inlay to both sides of the model, making the technique a bit more relevant.
For this example, I’m going to walk you through creating a simple multi-colored keychain, where the inlaid text is a second color that’s printed separately. However, note that you can follow the same workflow for just about any object – including complex shapes.
Be sure to stick around until the very end where I’ll demo the final 3D printed object.
To get started, I’ll create a new component in Fusion 360 for the Keychain Body.
I’m going to create a new box on the XY origin plane, with the dimensions of 50mm x 30mm and the height of 5mm.
I’ll add a fillet radius of 14mm to all four edges. Remember, if you need to select an edge on the other side of a body, you can always click and hold on the model, which will let you select the edge from the depth selector.
Next, I’m going to create a simple 6mm hole on the top of the keychain, which will be for a keyring.
I’m just going to eyeball the alignment, however, if you’re following along to make your own keychain, then you can always create a construction line to center align the hole.
We’ll also want to add a fillet of 1mm to the edges of the keychain.
We can now create a second component for the text. This is where you can create or insert any design that you want to inlay…it doesn’t have to be text. You could also use an SVG file to cut out a logo or more intricate design.
I’ll activate the text command and I’m going to select the top of the keychain as a face to sketch on. However, we’re going to cut this component out with the combine command, so it is not required that you sketch directly on top of the other component.
For my design, I’m going to type out the letters PDO, which is short for Product Design Online.
I would also recommend you find a font that has a thicker style or make sure to bold the text, as these letters are quite small. This will help ensure we have enough room to add a chamfer.
I’m going to select “Arial Black” and I’ll also make the text size 15mm.
Lastly, I’ll rotate the text and drag it into position, to the approximate center.
Before extruding the text, I’m also going to project the keychain shape. Later on, we’ll use this projected sketch to align the text on the opposite side of the keychain.
I’ll then extrude the text down -1.5mm…and we’re also going to want to set the operation to “New Body”
The reason I’m making this text its own component and separate body is so we can apply a draft angle or chamfer to the edges. The angled edge not only helps the inlay sit in place, but it generally provides for better print results.
If you do decide you want straight edges for your inlaid part then you can skip this step and instead simply extrude cut the text or your desired object out of the main component.
At this point, we can either add a draft angle or a chamfer. Generally, I use the draft command when creating inlays or similar projects like one-part molds. However, Fusion 360’s text command does not like to work with the draft command because of all the extra line geometry it produces.
Because of this, I’ve found that the chamfer tool produces much better results.
I’ll activate the chamfer tool from the modify dropdown list. Then, we’ll want to look at the bottom of the text.
Again, you’ll see that the text creates a lot of edges and faces. We can use a selection filter instead of selecting them one at a time.
In the select dropdown, I’ll find the “selection priority” flyout folder, and then the “Select Edge Priority”.
If you then look at the selection filters you’ll see that only “Body Edges” is selected. You’ll also want to make sure the “Select Through” option is unchecked, so we don’t accidentally select edges on the other side.
We’ll then need to look at the letters straight on, from the bottom view. We can use the selection window to drag over all three letters, which quickly selects all of those edge lines.
If we reactivate the chamfer tool, you’ll see that all of the selected edges are automatically applied as the “Edges”.
We’ll want to set the Chamfer type as “Two distances” which will give you greater control over the angle of this inlay.
For the second distance, I’ll type out 1.5mm, equaling the height of the text. This is to ensure that the cutout of the inlay runs to the edge of the letters.
For the first distance, you’ll want to play around with the value, to see what works best, as this depends on the font or type of object you’re working with.
If I try 1, you’ll see that my letters are quite thin in some areas. Instead of 1mm, I’ll try using 0.8mm.
0.8mm appears to work well. We can now turn the first component back on, or in this case, the keychain component.
When setting up inlays you may also find it helpful to throw on a quick appearance to help distinguish the two parts.
I’ll hit the keyboard shortcut letter “A,” as in Alpha, to activate the appearances dialog. I’ll search for wood, as I’m going to print the keychain with a wood filament.
I’ll drag and drop the hardboard appearance to the keychain.
For the letters, I’ll find a red or yellow plastic, as I want to customize the color to be orange.
Notice the orange letters are fuzzy because they’re on the same level as the face of the keychain. That will be fixed as soon as we cut those letters out with the combine body command.
I’ll activate the combine command from the “Toolbar”. It can also be activated from the modify dropdown or the shortcuts box.
For the target body, you’ll need to select your keychain or the body that will contain the inlay. For the tool bodies, you’ll need to select all of the letters or bodies that make up your inlay.
Then, most importantly, we need to change the operation to “Cut”.
We also want to check the “Keep Tools” option, as that will keep the text component after the cut operation is performed.
After clicking OK, you’ll see the orange letters are now fixed. We can also hide the Text component to double-check our inlay void.
Let’s now create the second cut-out on the opposite side before we work on adding clearance between the text and the keychain.
We’ll first want to copy the Text component in the Browser. Right-click on the top-level component and select “Paste New” which will create an unlinked copy.
Before clicking OK, we’re also going to reposition the text on the opposite side of the keychain.
I’ll first rotate the Y angle 180 degrees.
Next, is where the projected sketch will come into play. We’ll first want to turn on the sketch in the Browser.
Once the projected sketch is turned on, we can use it with the “Point to Point” feature. Select Point to Point as the move type, and then select one of the sketch points on the projected sketch.
Then, all we have to do is select the corresponding point on the keychain model. Notice how the copied text component then snaps into place, ensuring its in the exact location as the opposite side.
We can then turn the sketch back off as we no longer need it.
I’ll also select “Capture Position” so Fusion 360 knows we want this move to be permanent.
After clicking OK in the dialog, you’ll see we once again have the letters aligned with the same face as the keychain.
We simply need to follow the same steps with the combine command.
Select the keychain as the target body.
Select the letters or your object as the tool bodies.
The keep tools and cut options should also default to our last selection, so we can click OK.
Now that we have both sides cut out, we need to create a clearance between the parts.
To do this, I’m going to offset the faces of the text component.
I’ll hide the keychain component and the copied text component.
Once again, we’ll need to select many pieces of geometry. However, this time, we’re dealing with faces instead of edges. Therefore, we’ll need to change our selection filter to the “Select Face Priority”.
You can always check the “Selection Filters” to ensure only faces are checked.
I’m also going to look directly at the model so it’s easier to select everything.
We’ll need to click and drag with our selection box over all the bodies that make up the text.
Hit the keyboard shortcut letter “Q,” as in Quebec, to activate the Offset faces command.
We then need to deselect the top faces of the letters, so that we’re only adding a clearance on all sides that touch the keychain cutout.
Notice how the offset faces command won’t let us deselect faces. To fix this, we’ll need to switch the offset type from “Automatic” to “New Offset”.
It will then let us select the three top faces of each letter.
At this point, you need to type out the desired clearance. To get the best clearance you’ll want to print some test cubes to see how well your printer is calibrated. Generally, between .1 and .2mm works well for FDM printers.
For mine, I’m going to use the standard layer height of .15mm. Make sure that you also make this negative .15mm so the offset faces are moved inward.
One important thing to note with this process – sometimes offsetting many faces can bog down Fusion 360’s processor. If you have a lot of letters or a complex shape then you may want to divide up the task in sections.
If you turn the keychain sketch back on you can see the small clearance that we just added.
I’m also not going to worry about adding this to the copied text, as I’ll simply print these letters out twice.
Lastly, I want to show you one more trick that is useful when working with inlaid parts.
In some scenarios, you may have a design that has a negative cavity, where you didn’t create the initial positive portion.
For example, let’s pretend that I imported this keychain model and that I don’t have the 3D text component. Because the shape is unique with the chamfer, it would be hard to recreate it by guessing all the details. Instead, we can use the Boundary fill command to fill voids in a model, which can then be printed out as a different color.
Working with the boundary fill command requires a plane or surface to act as the “tool” or defined boundary.
We’ll first need to create a construction plane on the top of the keychain. There are several different construction planes that we could use. However, I’m simply going to use the offset plane, by setting the offset distance to zero.
I’ll then activate the boundary fill command from the “Create” dropdown.
For the tools selection, we’ll need to select the construction plane. Again, this doesn’t have to be a construction plane if you have another face that you want to define as the boundary.
For the second tool, I’ll select the keychain body itself.
Notice how immediately after the model turned green and these checkboxes appear. To create the letters, we’ll need to use the Cells selector to select all three letter checkboxes.
I’ll double-check the operation is set to “New Body” and then I’ll click OK.
We now have three new bodies that were created by filling the negative space or the void in the model. Again, this workflow is best when you have a model where the original positive wasn’t created to cut away the void.
At this point, you would want to follow the previous steps of offsetting the faces to factor in a clearance before you 3D print.
Let’s now take a look at the printed results! I’ve gone ahead and printed out the keychain in Hatchbox Wood filament and the letters in Orange PLA.
As you can see, the inlay and clearance work well together.
After gluing the letters in place I was also able to give it a quick sanding to make the final surface even smoother.
Last but not least, I want to give a shoutout to those who supported the channel over the last week by joining my Patreon or by contributing to my Buy Me a Coffee page.
Special thanks to the new Patrons…
Werner Berry, Todd Coello, Leo Moriarity, Alejandro Garcia, Bill Mac, Gene Uselman, Nigel Zett, and Tym Tucker.
And thanks again to those who bought me coffee….
Anonymous, Valentin, Bob T, Frank, Loren R, and John Sifers.
I hope you’ve enjoyed episode number 3 of practical prints! Be sure to subscribe if you’re not already, click the thumbs up icon if you learned something in this video, and click on that playlist in the lower right-hand corner to view the rest of the series.
Leave a Reply