In Fusion 360, Top-Down and Bottom-Up are two different methods in which you can combinePerforms boolean operations between solid bodies. Select the target body then select one or more tool bodies to perform a join, cut, or intersect operation on the target. More components to create an assembly. Both can be used, but this article explains the difference between the two and why you might want to use each. To understand each type, it is crucial to first understand assemblies and components as a whole.
What are Components and Assemblies?
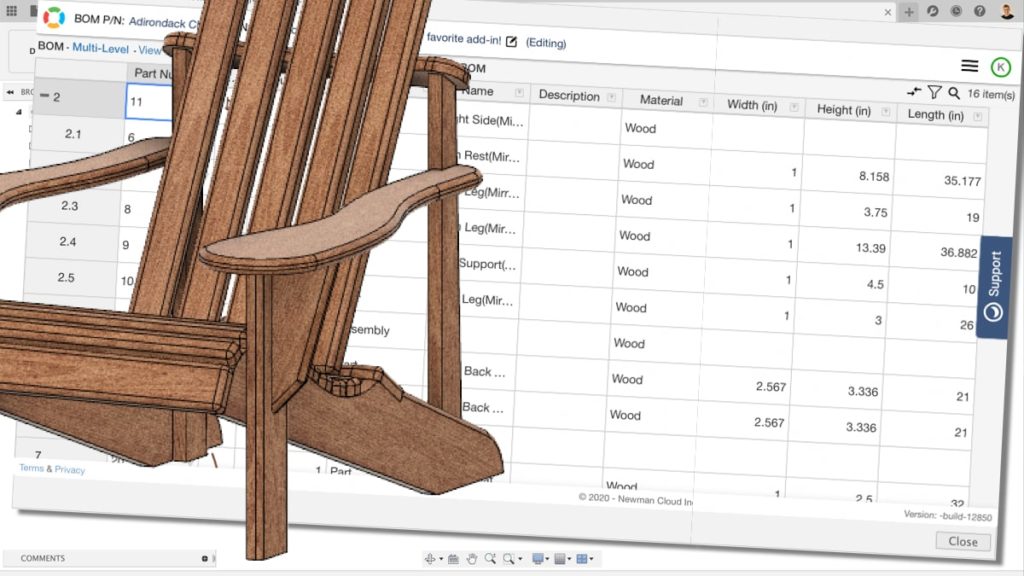
When creating a design in Fusion 360, each individual part that makes up a design is known as a component. A component is officially defined as a collection of data that makes up a single independently manufactured part.
Using a cake as an analogy, individual pieces of data such as 2D Sketches, Construction Planes, Canvases, and 3D Bodies can all be thought of as ingredients that, when combined by a “chef”, create a Component, or in this case, the cake’s sponge.
However, a cake is made of more than just a single sponge. Cakes are made up of several differently-sized sponges, icing, and decorations. Each of these different aspects of the cake can be thought of as a separate component and each has its own set of different ingredients. An assembly is created when all of the components are assembled together to create the finished cake.
Getting back on track, a Fusion 360 assembly is created when a group of two or more components is joined together within a design. An assembly can be created by combining different Fusion 360 files, or by using the “New ComponentCreates a new empty component or converts existing bodies to components. When creating an empty component, enter a name and select the parent. When converting bodies, select the bodies to convert. More” button within a single file, but both options result in a design that contains more than one component.
Bottom-Up Modeling
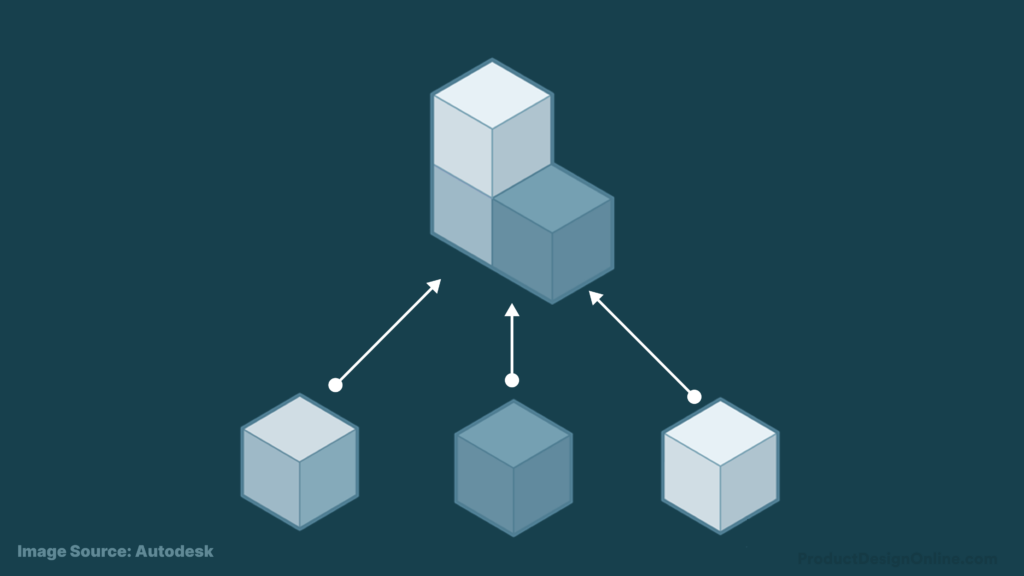
Bottom-Up modeling focuses on the individual parts that make up an assembly. Each key component is designed separately from the rest, normally in a separate design file. The geometry of one part is not typically influential on the other parts around it because they are all designed in isolation. (i.e. you start by designing the bottom-level components before combining them to end up with the overall assembly.) The design is completed by first designing the key components, and then assembling them together at the end.
Bottom-Up modeling is frequently used in software such as Solidworks, Inventor, and others which all have separate assembly file types. All components are modeled in separate part files, and once all the parts have been completed, an assembly file is created to join the individual components together. Bottom-Up modeling is also more common when using a large variety of standard parts because these do not need to be designed with other parts in mind and can easily be added to an assembly file at the end of the process.
Bottom-Up modeling is more common when there is only a small group or single person completing the design. When a large group is involved in a bottom-up modeling task it can sometimes be more difficult to communicate the design and ensure that the entire assembly fits together correctly.
Top-Down Modeling
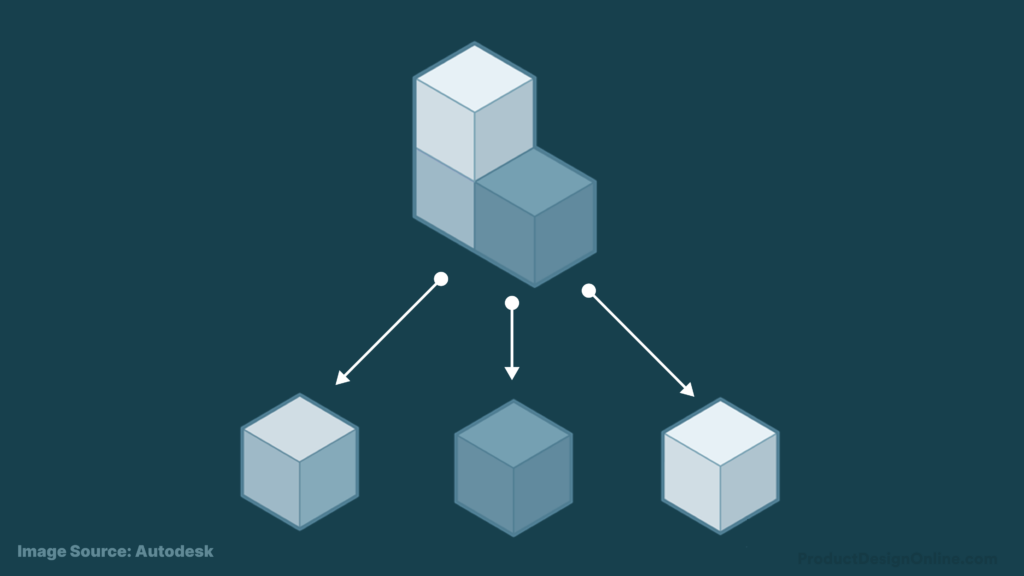
In Top-Down modeling, the focus is on the assembly, and the individual components are modeled around the entire assembly. With Top-Down modeling, you will have a single design file and each of the components will be modeled based on the references and geometry of its surrounding components.
Top-down modeling is common within larger teams, as one designer can easily design parts knowing that it will work correctly with a different component that was designed by a different person, as well as in the context of the entire assembly.
While bottom-up modeling allows for standard parts to be integrated, top-down modeling is more commonly used when a design contains all unique parts.
Which Should You Use?
Fusion 360 is designed to work with both top-down modeling and bottom-up modeling. The simple answer is that it depends on the application, and even then, a lot of designs make use of both at the same time!
Lots of teams will use Top-Fown for each of their sub-assemblies, and then use Bottom-Up to assemble the sub-assemblies together. This way designers can work on each sub-assembly at the same time
If you are using a lot of off-the-shelf components, you will probably end up using Bottom-Up within your design. If all the parts are custom-made, use Top-Down. Bolts, fasteners, and other fixings are all good examples.
Bottom-Up Advantages
- File Size
- Groups can all work at once in different files
- Use of standard parts
Top-Down Advantages
- References are always correct and can be easily linked. Changing one component will automatically change the others.
- You can work from someone else’s designs without issues
- Time saver – no need to re-draw sketches for reference
- All within one file, easier to edit and make changes
How to Use Top-Down and Bottom-Up Modeling
Bottom-Up: Create separate files for each component, Insert them into the current design, use joints to create an assembly, and use edit in place (or edit in the original component to make changes).
Top-Down: Create a single file with the name of the assembly. Start by modeling a core component and add new components to the previous one until the assembly is complete. Use component activation to edit each component correctly.
thank you
You’re welcome, Krish!
Best,
Kevin
Thank you, very well explained
Glad it was helpful, Dhananjay!
Cheers,
Kevin